Get the best value from your filling lines
Maintaining your equipment is key to long term success on your filling line, but how do you know what your machine needs? At SIG, we provide continuously improved corrective and preventative maintenance concepts and easy access to original and qualified spare parts for all SIG filling machines, applicators, and selected downstream equipment. With the right maintenance plan, you can:
-
Prevent or drastically reduce downtimes
-
Preserve the longevity of your equipment
-
Optimize costs, output, and time
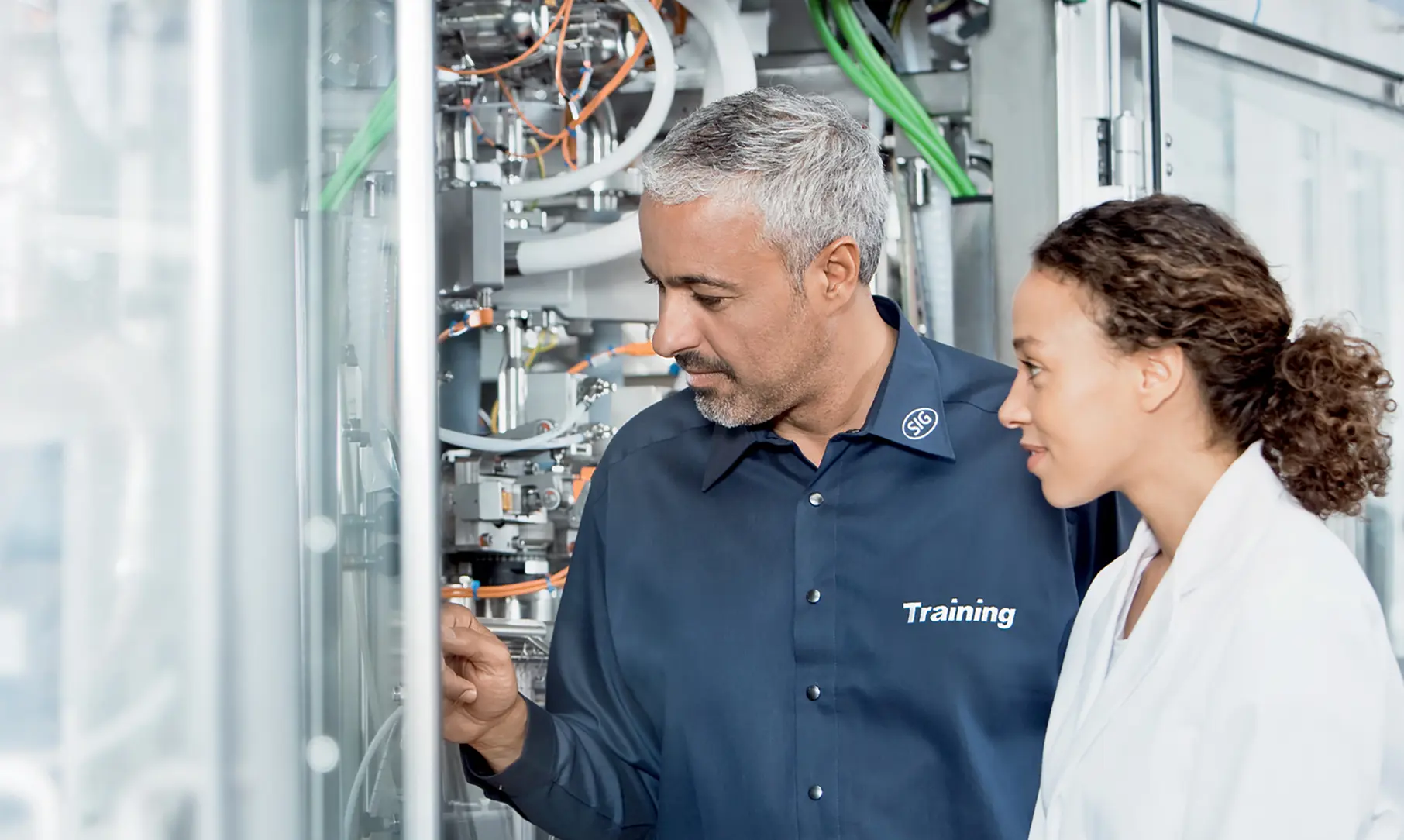
Diversified maintenance plans strategies to support you at all times

Preventative maintenance:

Corrective maintenance:

Production support:
Spare parts to keep you running
We offer spare parts for all maintenance tasks for SIG filling machines, applicators, and selected downstream equipment. We act as a one-stop shop, delivering your parts quickly and streamlining the ordering process through our spare parts shop, available online and open 24/7.
Here’s a look at our spare parts through the numbers:
- 27,000 material numbers permanently in stock, accessible via phone, web shop, or email
- 5,500 parts on hand for downstream equipment
- 24/7 emergency order hotline and taxi deliveries to get you parts quickly
- Parts available from more than 400 suppliers with all orders handled personally by our team
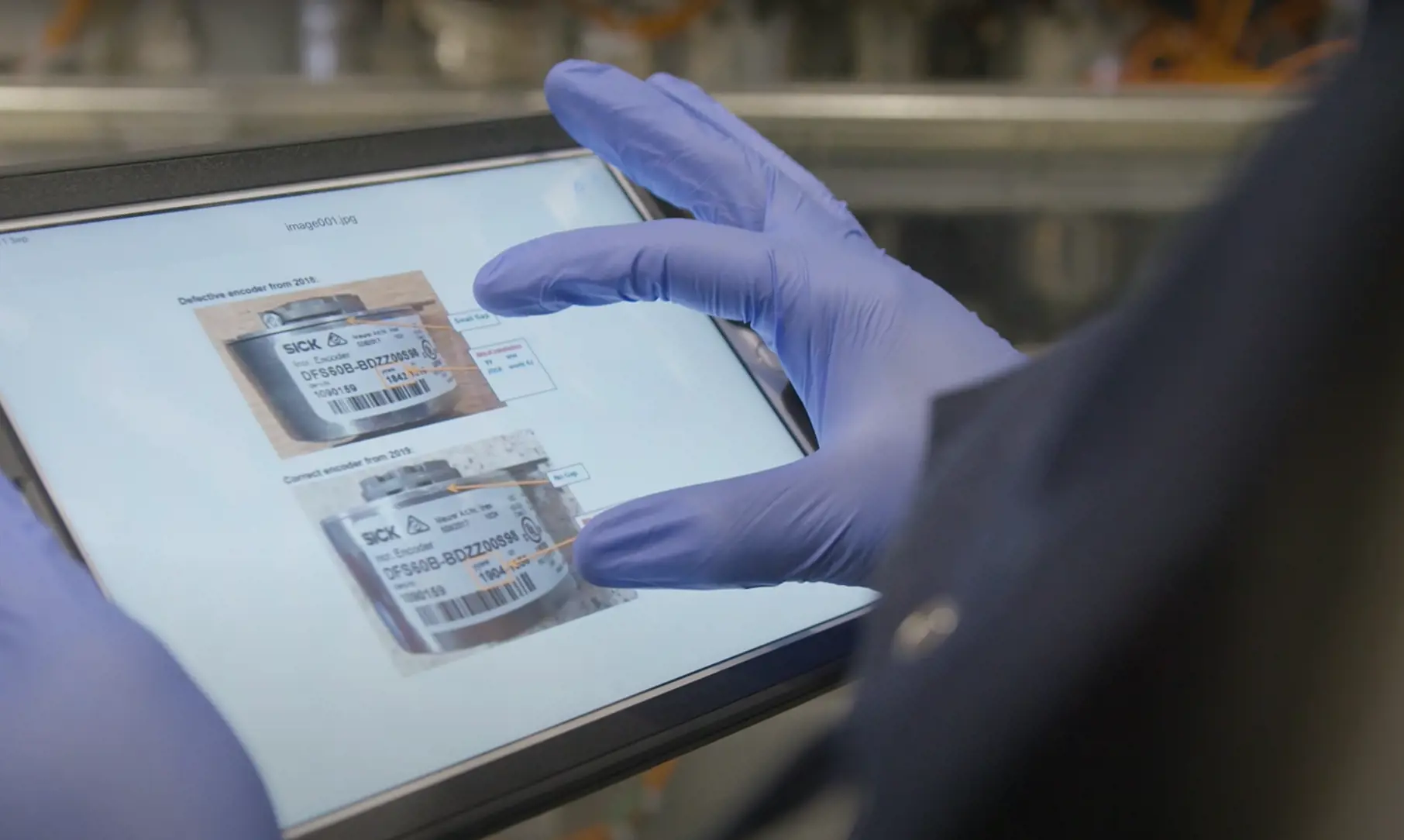
SIG Smart Maintenance - From reactive to proactive maintenance
For us, maintenance isn’t just a service we offer, but a process we’re always working to improve and optimize. Our aim is to catch issues before they arise so that our customer can concentrate to run their equipment. This is why we are striving to increase the amount of proactive service.
We’ve implemented digital tools that help us on that journey. We call this SIG Smart Maintenance.
We’re the first in the industry which integrated a Field Service Management and Asset Performance Management software to improve the way maintenance is being done. Our Field Service teams are equipped with tools and software that help them planning their actions and support them during their work on site. Digital documentation helps us to build a better understanding of challenges in the field and how to prevent issues for future.
Our Asset Performance Management software is a digital solution utilizing connectivity, cloud computing, and analytics to synchronize information from your filling machine and the work done on site to shift maintenance solutions from preventative to proactive (see also SIG Asset Health Monitoring).
We offer services globally and operate four reliability centers (in Brazil, Thailand, Germany, and Dubai) where we transform data into insights for our customers. By analyzing data, we can offer higher Overall Equipment Effectiveness (OEE), higher first-time fix rates, and proactive solutions to your maintenance concerns.
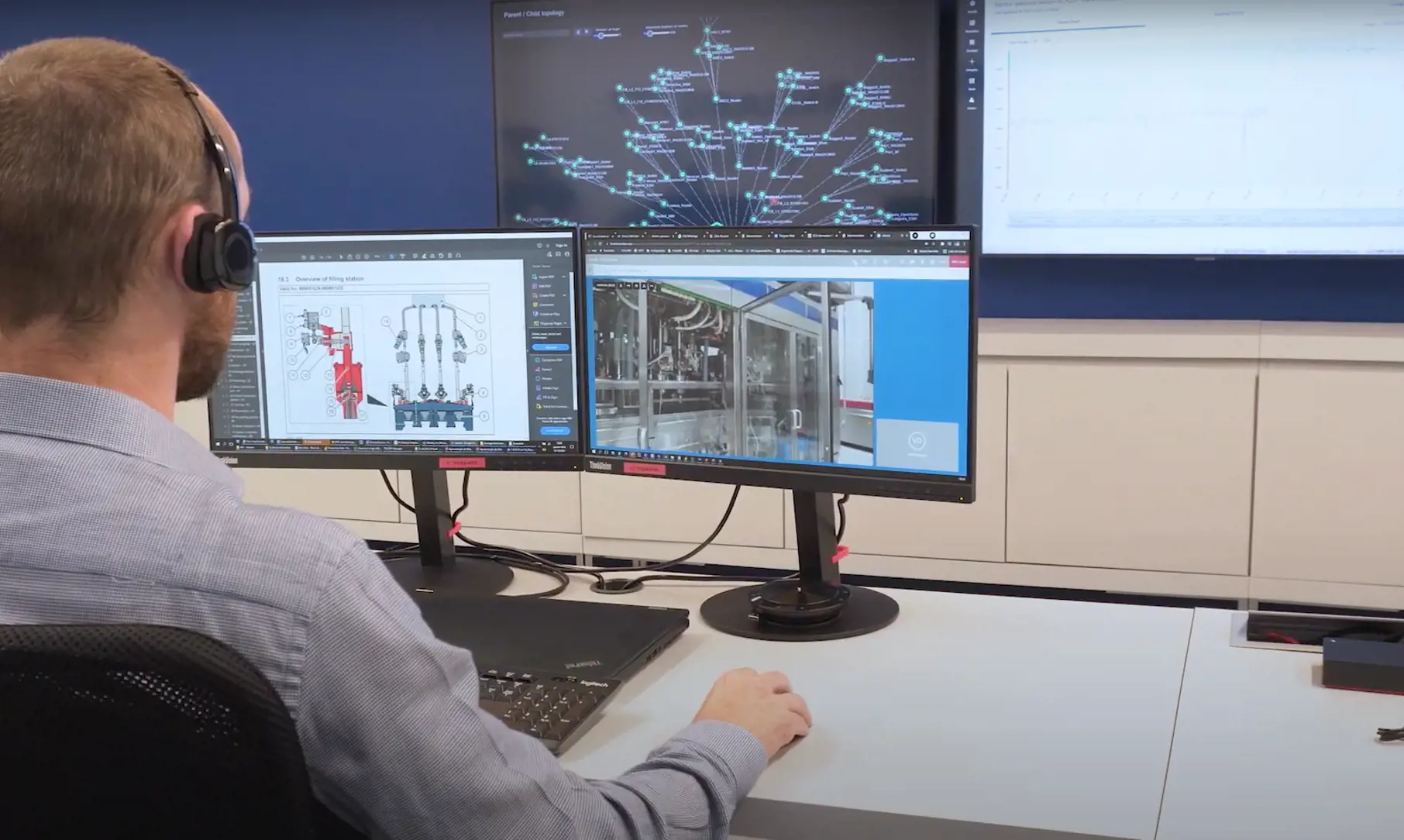
Learn more about how to shift your maintenance plan from responsive to proactive by getting in touch with an SIG team member now.