Turning paper into data
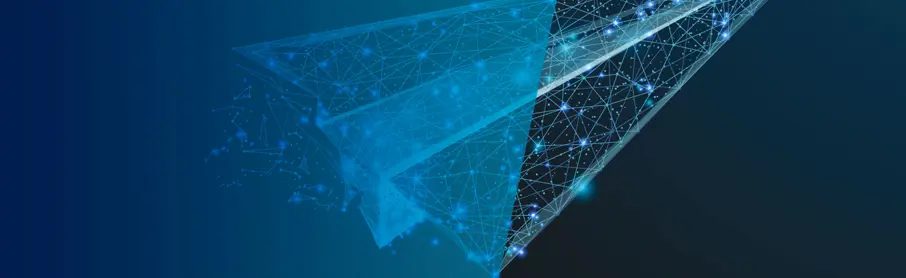
In part two of our new Co-Creating the Future series with GE Digital, we look at how and why manufacturers should make the shift from paper to data
In part one of our Co-Creating the Future series, we discussed how the food and beverage industry is ripe for digital transformation and a new era of innovation with SIG and GE Digital. Yet with many manufacturers still operating in a paper environment for information collection and reporting, the first crucial step is to move from paper to data. Traditional paper-based operating systems suffer from a number of issues but chief amongst them are speed, accuracy and traceability. Paper record management is inherently slow, with plant workers typically having to move between work stations, each time checking off boxes, filling out forms or copying down numbers. An increased number of manual processes often leads to human error. As no matter how experienced people are, they will inevitably make mistakes. This situation can be exacerbated when working across a range of equipment types within 24/7 operations, with multiple employees from different shifts potentially affecting the process over the course of a day. Paper-based information also exists in silos – what’s written on the paper exists only on the paper. But information within manufacturing plants typically needs to be archived, shared or analysed. And if manufacturers want to perform analysis on huge reams of paper, it can be an impossible task just to gather all the information needed in one place. All these factors create a complex working environment for manufacturers – not just on the shop floor but through all support and strategic levels, right up to senior management. Whether it’s real-time tracking or monthly reporting, managing the paper trail can be inefficient, time-consuming and simply overwhelming. This means lower quality, longer lead times and higher costs.
Reducing complexity
GE experienced first-hand the complexities of paper at one of its factories in Germany. They timed how long it took a worker to process an order for a part via paper. It was over 25 minutes. When they digitised the worker’s process, this 25-minute task became a six-minute task. He picked up a part and scanned a barcode, before performing his task and moving it onto the next stage of the process. There were no errors and the data could be shared and analysed to find further productivity and quality gains for the future. GE Digital is applying this experience, together with learnings from other industries, to the development of solutions for the food and beverage industry. “Industries like extraction and refining can be more asset intensive than most food and beverage operations, but that asset-centricity does provide some valuable operational and service data,” says Matt Wells, VP of Product Management at GE Digital. “GE has learned a lot about leveraging analytics to improve the uptime of critical assets and the impact of that on the entire plant. Furthermore, GE has made significant advances in the acquisition, storage, processing and security of all the data required to accomplish this uptime.” Managing data from diverse equipment and multiple suppliers is another key issue for GE. Their software applications can interface with a wide range of industrial equipment and protocols, either directly or through relevant standards like OPC. Their MES, Automation and ERP software is open, layered and ‘asset agnostic’, meaning it interfaces with all asset types regardless of supplier. This means that, together, SIG and GE Digital can not only create an entire plant solution but also seamlessly implement digital solutions on top of a customer’s existing technology. Ultimately, this will relieve plant workers from costly and inefficient paper data collection, giving them more time to address operating issues rather than simply identifying them. To see how manufacturers can apply this newfound wealth of data, don’t miss part three of the Co-Creating the Future series where we’ll examine how data can transform performance. Want to know more about SIG’s partnership with GE Digital? Contact us now or discover more about SIG’s Smart Factory solutions.
- settembre 07, 2018