The Smart Factory Journey
The benefits of a smart and connected factory are clear but how do you get there? We explore the key challenges and solutions to consider during the smart factory journey. Revolution or evolution? It’s a common debate...
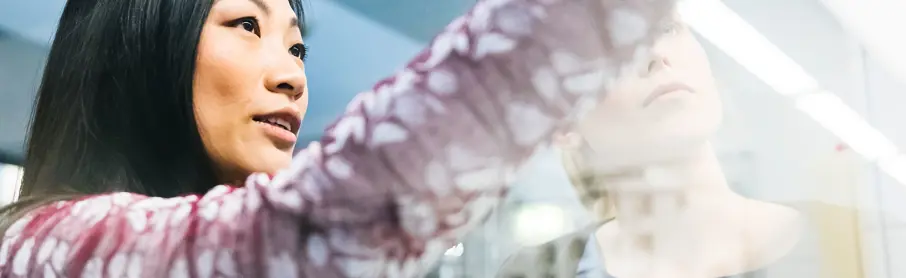
The benefits of a smart and connected factory are clear but how do you get there? We explore the key challenges and solutions to consider during the smart factory journey.
Revolution or evolution? It’s a common debate in manufacturing whether Industry 4.0 represents rapid transformation or gradual change. But no matter which way you look at it, what’s clear is that creating a smart factory doesn’t happen overnight. And just as every business is unique, so too is every smart factory journey. The major challenge is how, when and where to get started. This is particularly true for plants with equipment that comes from several different suppliers and with diverse technological capabilities. Many manufacturers are therefore faced with the problem of how to collect data from older machines while ensuring a common and connected data platform for the entire plant. In its report examining the smart factory journey, Deloitte outlines five key areas for manufacturers to consider and prioritise. These include how to use data, which technologies to implement, how to adapt processes, managing people and organisational change, and protecting against cybersecurity risks. To effectively manage these areas, Deloitte recommends businesses follow a step-by-step path. In this, plants can scale flexibly – from single assets all the way to a complete smart factory network. Manufacturers therefore need an evolving solution that enables them to not only integrate new technologies but gradually achieve agility, connectivity and transparency across the entire supply chain.Start and scale to your needs
The steady smart factory journey is being undertaken in all industries. Samsung Electronics, for example, is increasingly automating its manufacturing processes by tapping into technologies such as robotics and radio frequency identification. The company aims to complete its ambitious smart factory project by 2020. It is already seeing a more than 25% improvement in plant productivity. Within the food and beverage industry, manufacturers recognise the potential to optimise production efficiency, quality, costs and safety. Yet many are understandably cautious about making the right investment. That’s why SIG offers fully tailored smart factory solutions that enable businesses to change at a pace and scale to suit their needs. SIG has recently partnered with ProLeiT, a leading provider of automation and process control systems, to co-create innovative manufacturing solutions for food, drink and dairy producers. This collaboration means customers will benefit from Manufacturing Execution Systems (MES). These enable them to develop connected factories securing the highest efficiency, flexibility and quality. MES solutions cover an entire operation – from raw materials to finished products. With one open system, manufacturers can integrate processes, gain complete control of their production, increase efficiency and ensure transparent information at every level. And, crucially, MES solutions allow a plant to flexibly grow due to scalability and modularity. Ready to start your smart factory journey with SIG? Contact us now or discover more about our smart factory solutions.Pubblicato in
Contrassegnato in
Data di spedizione
- giugno 20, 2018