Seeing into the future
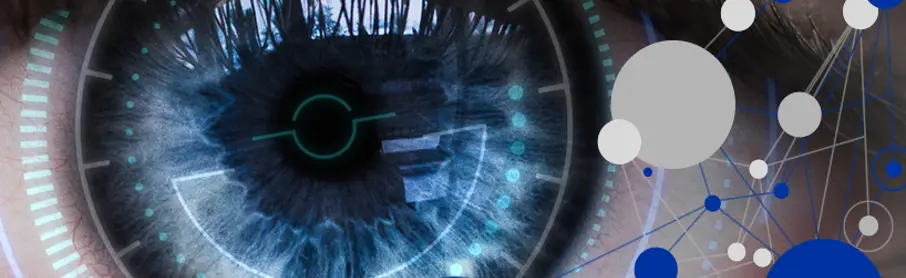
In part five of our Digital Discovery series, we delve into a growing trend that lies at the very heart of digital transformation – predictive maintenance
In part four of our Digital Discovery series, we examined the rise of logistics 4.0 – a new era of digital logistics in which transparency, efficiency and sustainability are transforming supply chain management. As we discovered, logistics 4.0 is all about making processes smarter and more streamlined. And these benefits are central to another growing digital trend: predictive maintenance, a market that’s set to be worth $10.9bn by 2022 – up 39% from 2017.
The power of prediction
In our earlier Co-Creating the Future series, we looked at how food and beverage manufacturers can start to move from inefficient preventative maintenance to intelligent predictive maintenance. The days of having to wait for a production plant to break down before it can be repaired are numbered. Now, intelligent systems can recognize faults before they happen, opening up the way to potentially huge cost savings and new ways of working.
So the question is, why aren’t all food and beverage manufacturers already utilizing predictive maintenance? Compared to other industries, the food and beverage sector has typically been a conservative adopter of digital trends. And a key reason for this is that the industry faces a number of specific manufacturing and maintenance obstacles – from strict regulations for food hygiene and safety to highly complex machinery that can be challenging to maintain.
A question of cost
Another significant barrier for manufacturers is simply cost. Integrating and establishing a successful predictive maintenance program often demands a high level of investment due to added smart sensors, components, monitoring equipment and more. But the long-term benefits for the bottom line are hard to ignore.
For US rail company Union Pacific, for example, predictive maintenance is thought to save them $100 million a year. And the potential for food and beverage manufacturers is equally huge. Less downtime means more active production hours. It means less maintenance and spare parts expenses. It means less time and energy. And it means critical assets can be constantly monitored to ensure problems are resolved before they even happen.
The right solution
Another critical consideration is choosing the right partner and solution. Manufacturers need a technology partner that can help them fully reap the benefits of predictive maintenance – turning a growing world of data into actionable insights that make a difference.
That’s why SIG partners with the leader in digital transformation, GE Digital, utilizing its Predix applications to accurately predict and optimize asset performance. The result of this partnership is our co-developed SIG Plant 360 Asset Management. It’s a solution that’s ultimately designed to help manufacturers operate machines for longer, boost productivity, lower costs, increase competitiveness and, crucially, ensure continual food safety.
Want to know about the latest digital trends? Look out for part six in our Digital Discovery series when we’ll recap all our stories so far and look ahead to the big trends in digital technology for 2020 and beyond.
To get more stories like this sent straight to your inbox, subscribe to the SIGnals Update, our exclusive bi-weekly newsletter.
- marzo 10, 2020