From paper to packaging
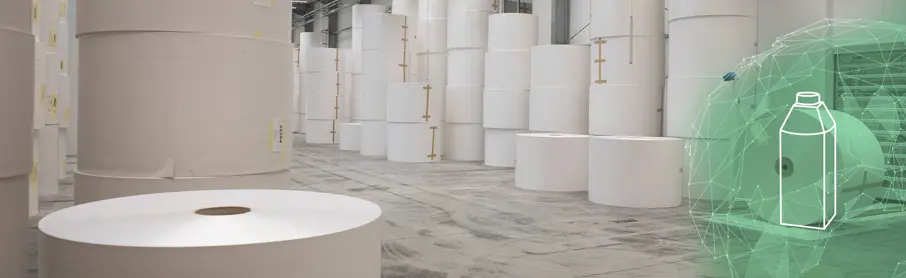
In part four of our World Behind the Pack series, we look at just what it takes to create our lightweight, protective and ready-to-fill carton sleeves
In part three of our World Behind the Pack series, we saw that meeting consumer needs isn’t just about creating packs that are convenient to use, transport and drink from. It’s also about ensuring the right structure of packaging material for the products they want. So how is this material actually produced? And how does an SIG pack start to take shape?
The benefit of sleeves
At our packaging plants around the world, we produce billions of preformed carton sleeves a year. Creating these sleeves takes a lot of expertise, effort and specialized processes. And they’re completely unique to SIG – ensuring an extremely high level of precision and consistency as well as a very low waste rate. And once ready, they’re sent out to our customers and are ready to fill on one of our aseptic filling machines.
Packaging that protects
It all starts with large rolls of paperboard which are first coated with an outer layer of high-quality polyethylene (PE) to keep it impermeable. A razor thin layer of aluminium is typically applied to protect the pack’s contents against light and oxygen. But we also offer innovative aluminium-free options with EcoPlus, SIGNATURE PACK 100 and Heat&Go. Another layer of PE is placed over any aluminium to bond it to the paperboard and prevent it coming into contact with foods or liquids.
Quality print and look
After coating, the packaging material is printed with up to six colors using a high-quality gravure printing system. This enables vibrant colors, flexible designs and innovative visual effects. Our carton packs are also designed to give brands and producers as much space as possible to communicate to consumers, with information, branding and artwork on all sides.
Precise in every way
The coated and printed carton is then cut to size for different formats before each one is stamped, creased and prepared for folding. The longitudinal seam is then sealed, which requires the ultimate precision. Crucially, this type of fold prevents any contact between the uncoated cut edge and filled goods. And it’s monitored throughout production to guarantee the highest levels of safety and hygiene. All that’s left is to pack these sleeves into boxes and distribute them to wherever our customers are.
Want to see all these processes in action? Then watch the film to see how our raw paperboard becomes ready-to-fill carton sleeves.
Want more stories like this sent straight to your inbox? Subscribe to the SIGnals Update, our exclusive bi-weekly newsletter.
- marzo 02, 2020