The power of digitalisation
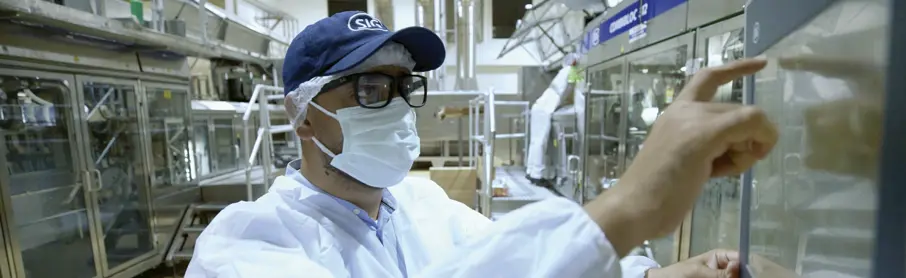
In part three of Ultimate Factories, we explore how data-based insights are transforming factories powered by digitalisation.
As we stand on the verge of Industry 5.0, digitalisation in manufacturing is more than a buzzword. It is the reality that is helping drive bottom lines. But what does smart manufacturing and digitalisation of production processes really mean in the food and beverage industry, and to what extent does a factory have to be digitalised to stand out?
Tech takes the lead
Smart manufacturing can be loosely defined as a technology-driven approach in which components in the manufacturing process share information digitally to improve performance. These components could be factory machines or stakeholder systems across the supply chain, and the data they share can be used to identify gaps and improve processes.
Among the most-adopted digital manufacturing initiatives are predictive maintenance, quality checks, predictive efficiency, energy efficiency, digital twin technology for fast prototyping, and real-time asset tracking.
Making data count
Data collection in manufacturing is nothing new. Historically, factories have recorded data relating to their operations, but this data was used to examine failures after they occurred, much like an airplane black box after a crash. But unlike the aviation industry, which has faced challenges around live black-box data, the food and beverage industry has made huge advances in using real-time data-based insights.
Digital tools driving efficiency
A case where digitalisation proved to be transformative can be seen at Juhayna Food Industries. To decrease operating costs and improve overall line utilisation, Juhayna required data relating to overall equipment effectiveness, line monitoring, and capacity utilisation. Using digital tools and our SIG Excellence System (SES+), line utilisation and productivity both increased by more than 8% within five months.
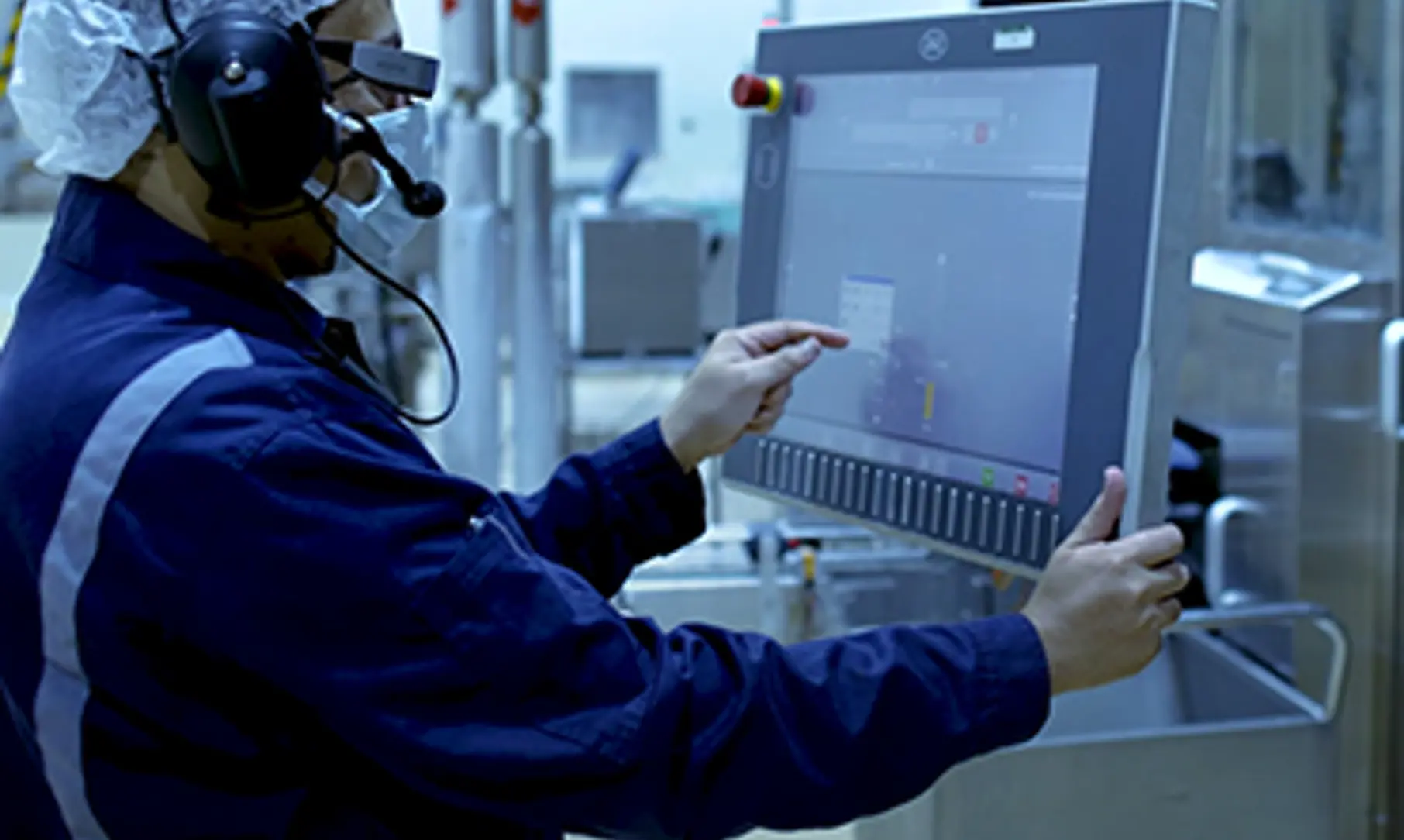
Asset monitoring for operational excellence
Effective asset monitoring increased productivity by 5% and line utilisation by 30% at Almarai, the Middle East’s largest food and beverage manufacturing company. With SIG Plant 360 Asset Management, it was possible to gain insight into daily operations while getting an overview of filling line health in real time. This helped reduce equipment downtime and improve preparation time during production.
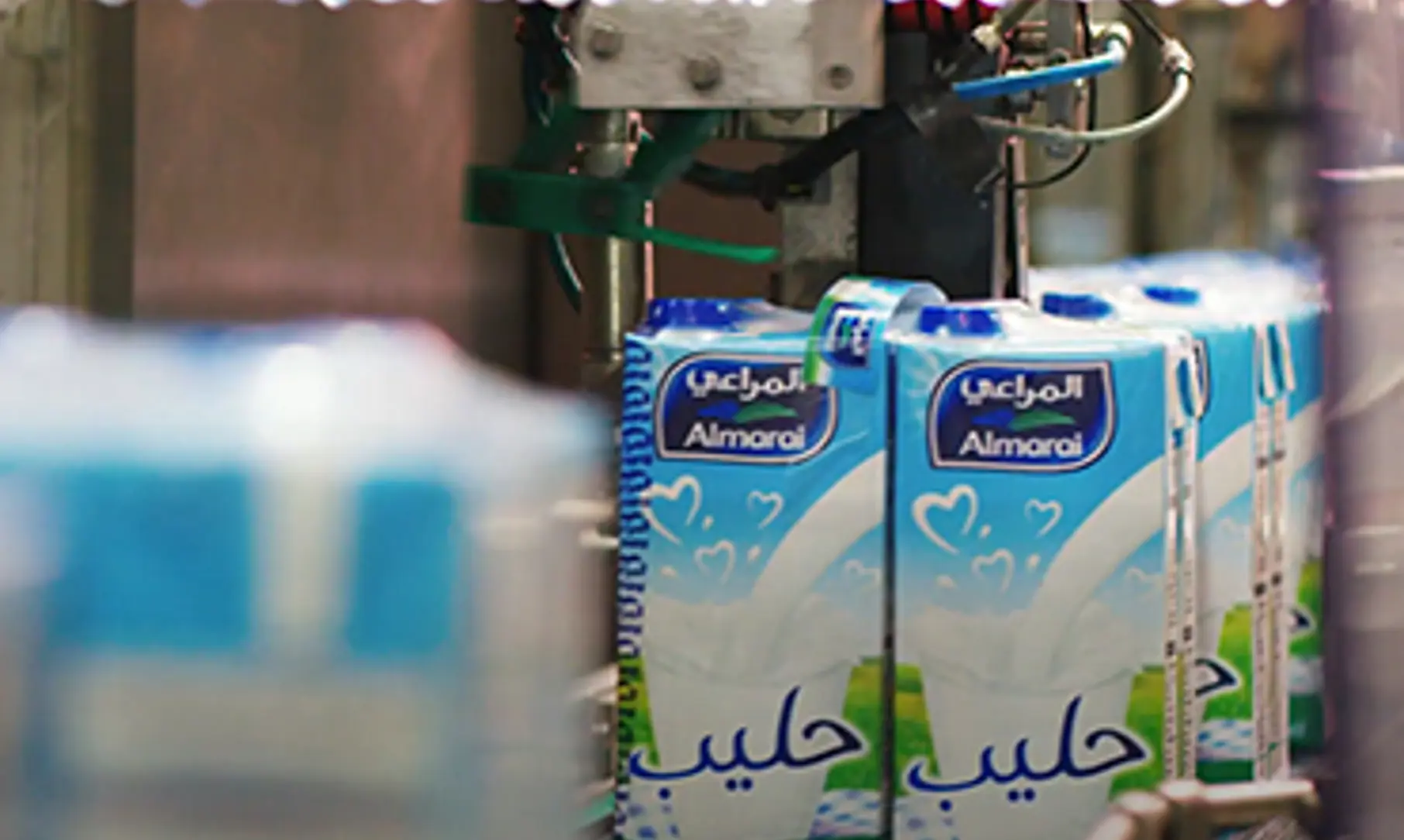
By monitoring key data from critical components, anomalies can be detected and mitigated in real time. And as we at SIG take monitoring even further with our Asset Health Monitoring system, our remote services can help mitigate any unplanned downtime as soon as issues occur – driving efficiency even further.
A digital path to the future
Manufacturers are increasingly turning to technology to gather more data about their facilities to streamline operations, increase efficiency, and be more adaptable to changing consumer needs. Therefore, finding the right partner is vital. And this is where SIG can help. Reach out to discuss how we can take your food and beverage plant to the next level of digitalisation.
Our commitment to enabling our customers is evident in all our service offerings, the latest being mySIG PORTAL, a digital platform enabling seamless collaboration, real-time communication and process automation all to help drive business forward for our customers.
Apart from digitalisation, flexibility in production is another critical factor that helps manufacturers respond quickly to both changes in supply chain and market demand – and we will explore how it can be a key differentiator in the next part of the series. Subscribe to our exclusive bi-monthly newsletter SIGnals Update so you don’t miss out.
- September 29, 2022