Breaking down the aseptic process
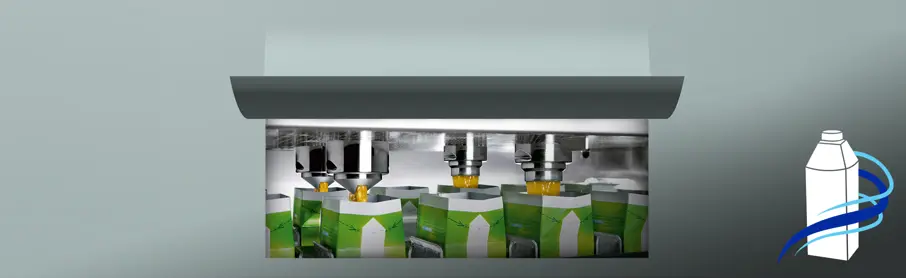
In part three of Aseptic Advantage, we look at the aseptic filling process and how it makes shelf stable products possible.
Aseptic packs have played a vital role in the evolution of the food and beverage industry, including vast improvements to food security and safety. In part two of the series, we looked at the science behind an aseptic carton. But there’s more to it than the pack – what is aseptic filling technology and how does it ensure food safety in ambient temperatures?
A three-step process
The aseptic process can be broadly defined as filling of sterilized products into sterilized packaging – under sterile conditions.
In the first step, the food or beverage goes through rapid thermal treatment to ensure that all harmful bacterial are eliminated and the product is commercially sterile. The now-sterilized product is then immediately cooled to a temperature suitable for filling.
The next step, that happens parallelly, involves sterilizing the packaging itself. With SIG’s pre-made sleeves that come with longitudinal seams hygienically sealed, the cartons are shaped in seconds before being heated, sterilized, and dried – and made ready for filling.
The third step involves putting the sterile product into the sterilized carton pack before ultrasonically sealing the carton above the filling level.
From sleeve to carton with #SIG
Different strokes
The type of thermal treatment used in aseptic processing differs depending on the type of food and beverage being packed – be it dairy, juices, nectars, or products with particulates.
Additionally, factors relating to the composition of the product also affect the length of treatment as well as the temperature setting. The focus, however, remains the same – ensuring a high-quality product that is commercially sterile and shelf stable with minimal loss to sensory qualities and nutrients.
The machine matters
The compact aseptic filling lines ensure sterility and compliance to the highest food hygiene standards. And as most manufacturers package multiple products in different formats, they need their aseptic filling lines to deliver on multiple fronts: flexibility, speed, efficiency, running time, and cleaning efficacy, among others.
The SIG edge
SIG’s range of aseptic filling lines deliver on all these factors while also offering the industry’s lowest waste rate – at less than 0.5% – and also have the highest level of flexibility in terms of format, volume, design and product type. And our newest filling line, SIG NEO, raises the bar even higher with the industry’s lowest carbon footprint, highest output per hour and automated cleaning – helping manufacturers save up to 30% in operating costs while ensuring best-in-class sterility and filling accuracy.
The latest advancements in aseptic technology are helping manufacturers achieve efficiency while maintaining product quality and their bottom line. But can aseptic cartons play a role in meeting society’s environmental and socio-economic challenges? Let’s explore that next time. Subscribe to SIGnals Update, our exclusive bi-weekly newsletter to get part four of the series and more straight in your inbox.
- May 12, 2022