The monomaterial edge
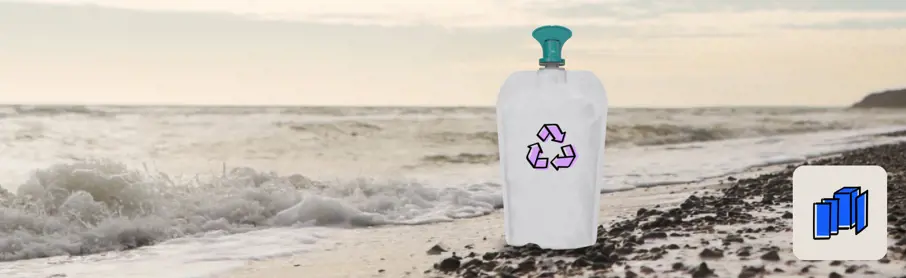
Monomaterial – the name says it all. Any packaging that is made of a single material is referred to as monomaterial. And that includes paper, glass, plastic, fabric, and other materials. But what is so new about it?
The answer lies in the fact that most packaging is made up of more types of materials than it is visible to the naked eye. Take metal cans, which are lined with a thin layer of plastic or flexible packaging that is made up of multiple layers of different types of plastic or altogether different materials.


For the purpose of this blog, we will look into the specifics of monomaterial film that is changing the face of flexible packaging.
The material
Monomaterial films are generally made up of polyethylene (PE), polypropylene (PP), and regenerated cellulose fiber (RCF). Among these, polyethylene is the most commonly used polymer for monomaterial, especially in food and beverage, due to its high strength, flexibility, and resistance to moisture. Polypropylene is also another widely used polymer that can be found in monomaterial films.
The process
We already discussed how plastics are made in our earlier post. For monomaterial films, the process usually includes blown film extrusion or machine direction orientation, a process that is gaining popularity in creation of monomaterial packaging called MDO-PE.
The circular advantage
Easy recyclability is the primary reason behind the creation and adoption of monomaterial packaging. Recyclable by design, monomaterial packs do not require any additional effort at the recycling end to be repurposed into post-consumer recycled (PCR) material.
Monomaterial keeps recycling costs down, making circularity more economically viable. Also, PCR can be recycled many times, aiding circular economy further.
The challenges
The material does not come without challenges and continued innovation in this area is key for widespread adoption of monomaterial in flexible packs. The key focus areas include production speed, sealing properties, adhesion, and leak proofing with fitment attachments.
At SIG, heating and cooling is done in the same step during pouch production to increase productivity and enable leak proof seals. Also, diamond-shaped seal boats for spouts help further sealability. Induction sealing also helps improve production speed without putting stress on the film.
The guidelines
Technically, monomaterial should be made of only a singular material. For plastic-based flexible packaging, however, there are guidelines backed by recycle testing that allow multi materials to be used. For a pack to be classified as monomaterial, the packaging film should contain more than 90% of one polymer type with the remaining elements being adhesives, barrier materials and inks.
Presently, SIG is launching three monomaterial solutions as part of its film portfolio – all the three solutions have passed extensive recycle testing and offer added barrier, durability, or both properties.
Monomaterial is more than a trend. The shift is likely to grow steadily with innovation addressing the residual challenges and making the material more sustainable.
In the next edition of Material Matters, we will talk about the most common metal in food and beverage packaging – aluminum. If you are not already subscribed to our newsletter, now is the time. Never miss another story from the SIG blog with our exclusive bi-weekly newsletter.