Smart factories that stand out
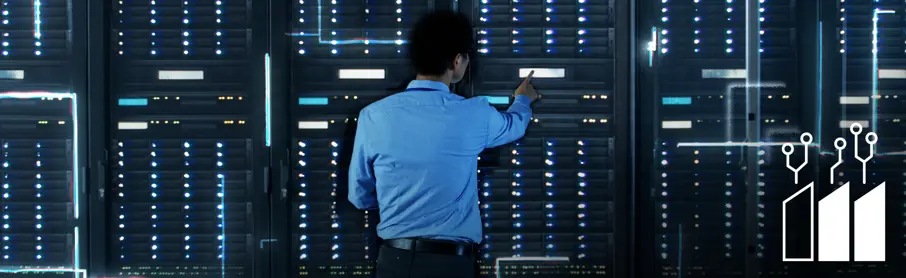
In our new series Ultimate Factories, we focus on smart factories that are pushing the boundaries of what’s possible within various industries – with a focus on food and beverage.
As the world has gotten smarter so has its factories – in terms of their carbon footprint, their flexibility, and their gradual adoption of automation and digitalisation.
And so, as smart manufacturing becomes more popular, we’re seeing more and more progress being made in the field. Such as the spread of predictive maintenance throughout a number of industries, thanks to Industry 4.0 making it cheaper and more accessible.
What’s new on the smart factory block?
With ongoing advances in automation, manufacturers can access more in-depth data from their machinery. This, in turn, is enabling process optimisation across the board, resulting in everything from a more sustainable production process to greater productivity – with less effort from everyone involved.
And with research showing smart factory initiatives could help the global economy grow an extra $2.2 trillion by 2023 – thanks to productivity gains – the only way is up for smart factories. As further evidence of this, the “Big 5” group of countries are on course to invest more than $101 billion into the smart factory market by 2025. So, how does that translate on the ground, and how is it helping manufacturers reap a host of benefits – from working more efficiently to reducing their environmental impact?
Thinking ahead
When it comes to smart factories that stand out, one of the main threads that connects them is their ability to scale up. Meaning no matter how big your production gets, the smarter your factory is, the easier it’ll be to manage things like human-machine collaboration and the collection of data. And that’s not to mention being able to keep efficiency and sustainability at the core of your operations, whatever changes occur.
A great example of the latter is SIG’s second state-of-the-art production hub in Suzhou, China, which has been built with expansion in mind: by 2024 the plant is expected to be 120,000 sqm in size, and, even now, has designed its roof to include enough photovoltaic panels to generate 1.5 million kWh of solar energy. As well as enabling smarter use of energy, the factory is using smart technology to improve sustainability elsewhere: like reusing treated rainwater for various procedures, with an aim to save approximately 28,000 tons of tap water a year.
In the second part of the series, we’ll place all our focus on automation within smart factories and how it is being put into practise. Follow along by subscribing to SIGnals Update, our exclusive bi-weekly newsletter.