Optimising resources
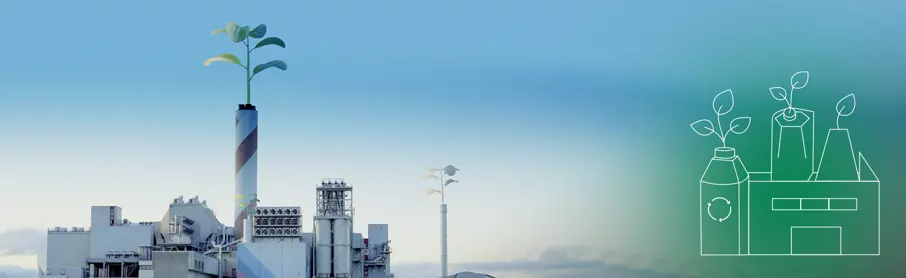
In the third part of our Sustainable Factories series, we turn our focus to resource optimisation. What is it, and how can it help manufacturers achieve greener operations?
In our previous story, we detailed how to design a sustainable factory from the ground up – from choosing the right site, to only using renewable energy sources. Now, we discuss how to implement each step correctly: by optimising resources.
Resource optimisation is the name given to the process of ensuring that labour and non-labour resources are aligned, with resources including labour, plants and equipment, materials, and suppliers. So, how can this be achieved?
It could be as simple as making sure machinery and other equipment is strategically positioned on the factory floor. For example – and as anyone working in manufacturing will know – when preparing goods for delivery, it makes sense to place goods right by a loading dock, thereby limiting how many trips employees have to make to transport items into trucks.
It could also mean creating a direct pathway on the factory floor so that forklifts can move goods quickly and easily, saving operators time and effort on the job. Overall, the design of a factory is hugely impactful to your supply chain, because, simply put, you want staff to have easy access to their workstations.
Inside elements
Other factors to consider when creating an efficient and sustainable factory environment include air quality. This could mean switching to cleaning products and paints that do not contain volatile organic compounds, or reducing chemical emissions during manufacturing – perhaps by incorporating a wet scrubber into your plans. Designed to remove carbon from gases released during industrial processes, wet scrubbers can also help optimise floor space by removing the need for manufacturers to buy extra filtration systems.
It could also be as simple as upgrading your HVAC systems, or choosing an environmentally friendly flooring system – one that doesn’t require buffing, stripping or waxing. Thereby, further limiting the number of chemicals used during day-to-day cleaning and maintenance.
The right supplier
Elsewhere, for real impact, you might consider making it a point to be more aware of the suppliers you work with. Because, if you ensure minimal pollutants during production and have a well thought-out and efficient factory floor, it makes sense to also be aware of the raw materials you use.
One way to verify suppliers is by using a pre-qualification check. Do they use a certified environmental management system, and what’s their record when it comes to complying with green laws and regulations? Where does the supplier buy their materials from, and are said materials sustainably sourced? Additionally, you could recommend to current suppliers that they themselves adopt more sustainable practices.
The digitalisation drive
Capitalising on Industry 4.0 is yet another way to optimise resources. Here, you could use digital technology to gain greater insight into your machinery, using data to improve the way you use equipment. This can extend the lifecycle of equipment and help factory staff work more efficiently. You could also use digital tools to track and trace products, helping catch problems quickly in order to limit waste.
The path to sustainability
Clearly, there are some challenges to executing these steps efficiently, not least of which is deciding what to prioritise, and what order to follow. Which is where the right partner comes in. At SIG, we are determined to help manufacturers become as efficient and sustainable as possible. Take Plant 360 Asset Management, our asset performance optimisation solution – enabling manufacturers to optimise their filling line availability and reliability while controlling costs.
In part four, we’ll take a deeper look into our Plant 360 solutions and how they can help improve the way manufacturers monitor energy and water consumption, sourcing, and waste output – the four categories that make up sustainable manufacturing.
Want more stories in the series sent straight to your inbox? Subscribe to the SIGnals Update, our exclusive bi-weekly newsletter.
- tháng 3 30, 2021