Green from the ground up
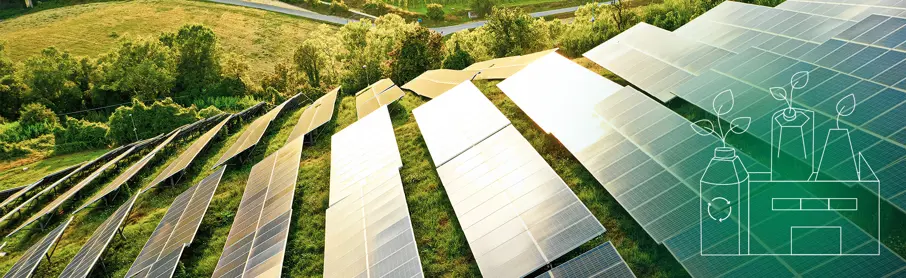
In the second part of our Sustainable Factories series, we detail the steps manufacturers can take to build and run factories that minimise their impact on the environment
How do you design a factory that’s more efficient across the board? A factory which supports an overall smoother supply chain where you can produce more high-quality goods – quicker – all while reducing your environmental impact?
With a sustainable factory, it’s possible. But getting there takes several steps. An essential place to begin is with the factory site itself. Because to be truly sustainable, you must also consider the environment around you, which means ensuring construction is carried out with as little impact as possible.
This includes reducing pollution during building or renovation, making sure the project protects and preserves the surrounding habitat and natural resources. It also means ensuring your plans include a stormwater drainage system, both to improve on-site infiltration and reduce the impact on natural water systems.
Turning the spotlight on renewable energy
But there’s much more to it than this. The growing partnership between renewable energy and Industry 4.0 also plays a vital role. And so, with industrial heating and cooling applications accounting for a sizeable chunk of global energy consumption, using the IIoT to produce more energy-efficient systems has a large part to play in helping manufacturers shift to a sustainable factory model.
For some manufacturers, this has meant using electricity generated from renewable energy sources to provide heat. Referred to as “renewable power-to-heat”, this requires manufacturers to, for example, introduce electric boilers to their factories, the likes of which can heat water to be used for space heating.
It could also mean turning to heat pumps, which can transfer heat to factories by using natural sources such as air, water and the ground. The signs are already pointing to worldwide adoption of the latter: according to IRENA, heat pumps are expected to supply 27% of the global building industry’s heat demand by 2050.
The potential of biomass
There are other sources, too. Within renewable energy sources, biomass – which can come from wood, straw, manure, and even algae – has great potential. However, industries can face challenges in finding biomass that has been sourced sustainably, and which is low-cost. One way to limit the environmental impact of biomass, which produces CO² when burned, is to replant trees. Here, it’s also important to note that CO² produced from biomass is already part of the planet’s natural carbon cycle, as opposed to CO² produced by fossil fuels.
Chain reaction
Looking outside of renewable energy sources, manufacturers can also make changes on a more immediate level. If we look to food and beverage manufacturers, this could mean working exclusively with suppliers who themselves are sustainable. It could also mean constructing factories out of eco-friendly materials, updating recipes to remove unsustainable ingredients, and introducing environmentally friendly cleaning practices – among many other steps.
A good example of this is Clif Bar & Company. In 2016, the company opened a bakery that incorporates sustainability at every step: with walls made of recycled barnwood and natural stone, hybrid cooling towers, LED lighting and a water source heat pump. And that’s on top of ensuring the bakery followed an overall biophilic design – meaning it’s been designed to make employees feel closer to nature.
Green teamwork
With so much potential available, food and beverage manufacturers need partners with expertise in sustainability solutions. At SIG, we’ve never stopped working on ways to make our own facilities more sustainable, with the results starting to show. Take our Asia-Pacific Tech Centre in Suzhou, China, built in 2019. With rooftop solar panels, low-flow sanitary fixtures, wastewater reuse and rainwater collection, the centre offers a clear example of our ability to help manufacturers transform their factories from the ground up to make them operate more sustainably. As a result of our work here, the centre is only the ninth industrial company in China with onsite manufacturing facilities to earn LEED Platinum certification. With a total of 83 points, the centre has the second highest score in the country.
Taking all the necessary steps into account, the next question we need to ask is how manufacturers make sure they are implemented correctly. And that means considering resource optimisation. How are food and beverage manufacturers improving the way they use labour and non-labour resources, and can this lead to more sustainable factories? Furthermore, what challenges must be overcome to optimise these resources, and how can SIG help? Find out in part three of our series.
Want more stories in the series sent straight to your inbox? Subscribe to the SIGnals Update, our exclusive bi-weekly newsletter.
- tháng 3 03, 2021