Enabling the green shift
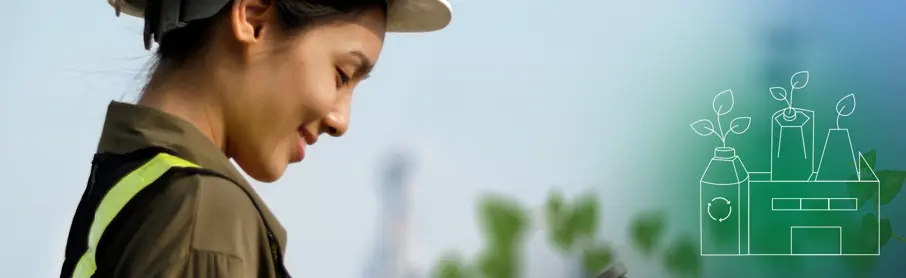
In part four of our Sustainable Factories series, we discuss how improved monitoring and control can help manufacturers create greener factories.
In part three of our series, we discussed how resource optimisation is helping industries and manufacturers embrace a more sustainable supply chain. But, to get there, manufacturers should first look at the following factors: energy, sourcing, water and waste.
Energising change
In 2018, 37% of global final energy use was attributed to industry – a 0.9% increase year-on-year since 2010. And so, to meet growing consumer demands while achieving energy efficiency, manufacturers could use an energy management team to audit any systems that use water, air, gas, electricity and steam. By gathering insight on energy consumption across the entire supply chain, this can enable optimal peak load management.
Green sourcing
Between the cost of natural resources and growing environmental awareness, manufacturers are beginning to understand the importance of controlling and monitoring their resources. For the food and beverage industry, food and packaging are two key factors to consider. With SIG’s Track & Trace solution, manufacturers can monitor products over their entire lifecycle, from farm to fork.
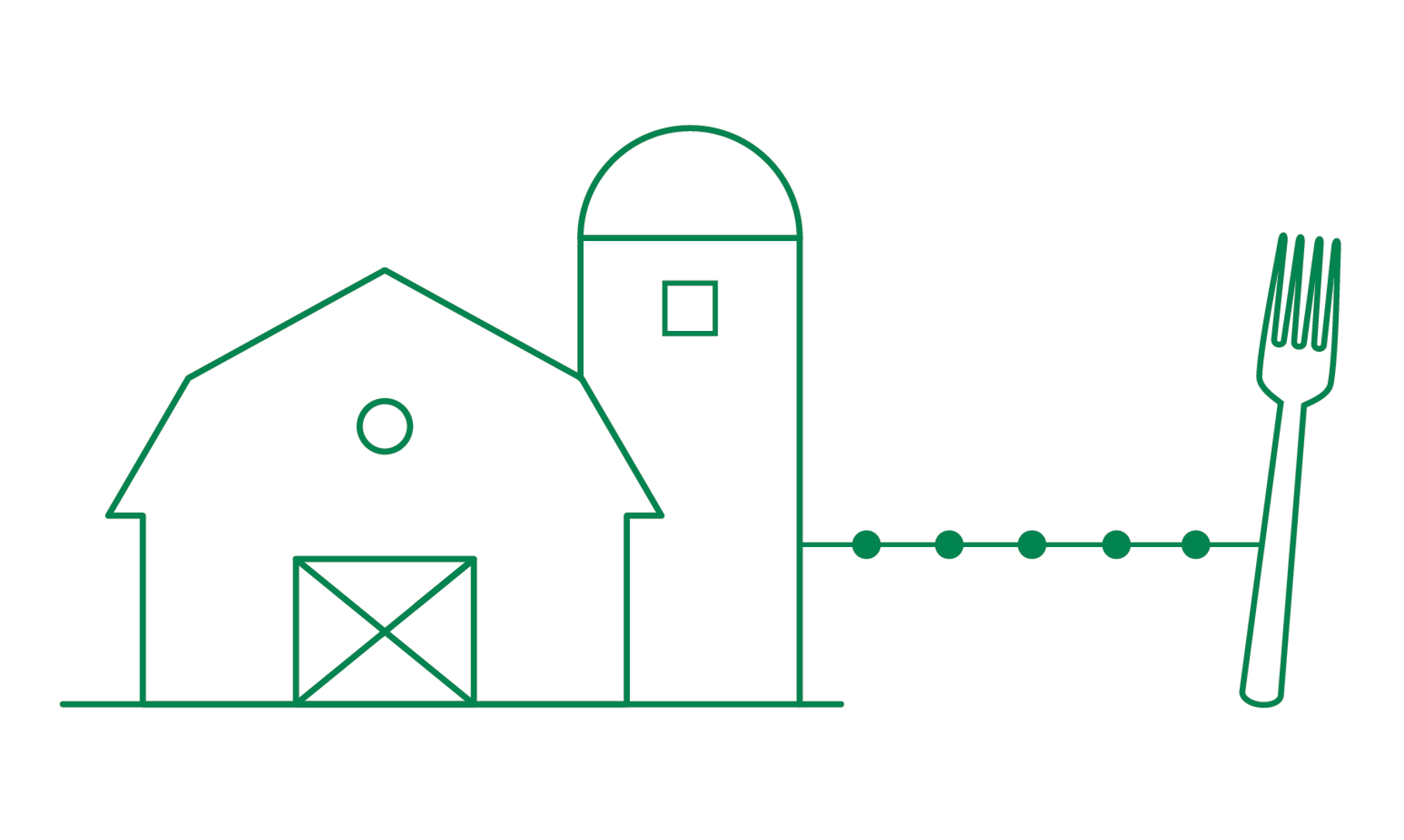
Covering every angle
SIG’s Plant 360 Controller is another tool designed to support green business practices, allowing manufacturers to keep a close eye on every aspect of their production process. With Plant 360, manufacturers can connect equipment under one system and gather data in real time, giving them the opportunity to optimise output and scale up production in a sustainable manner.
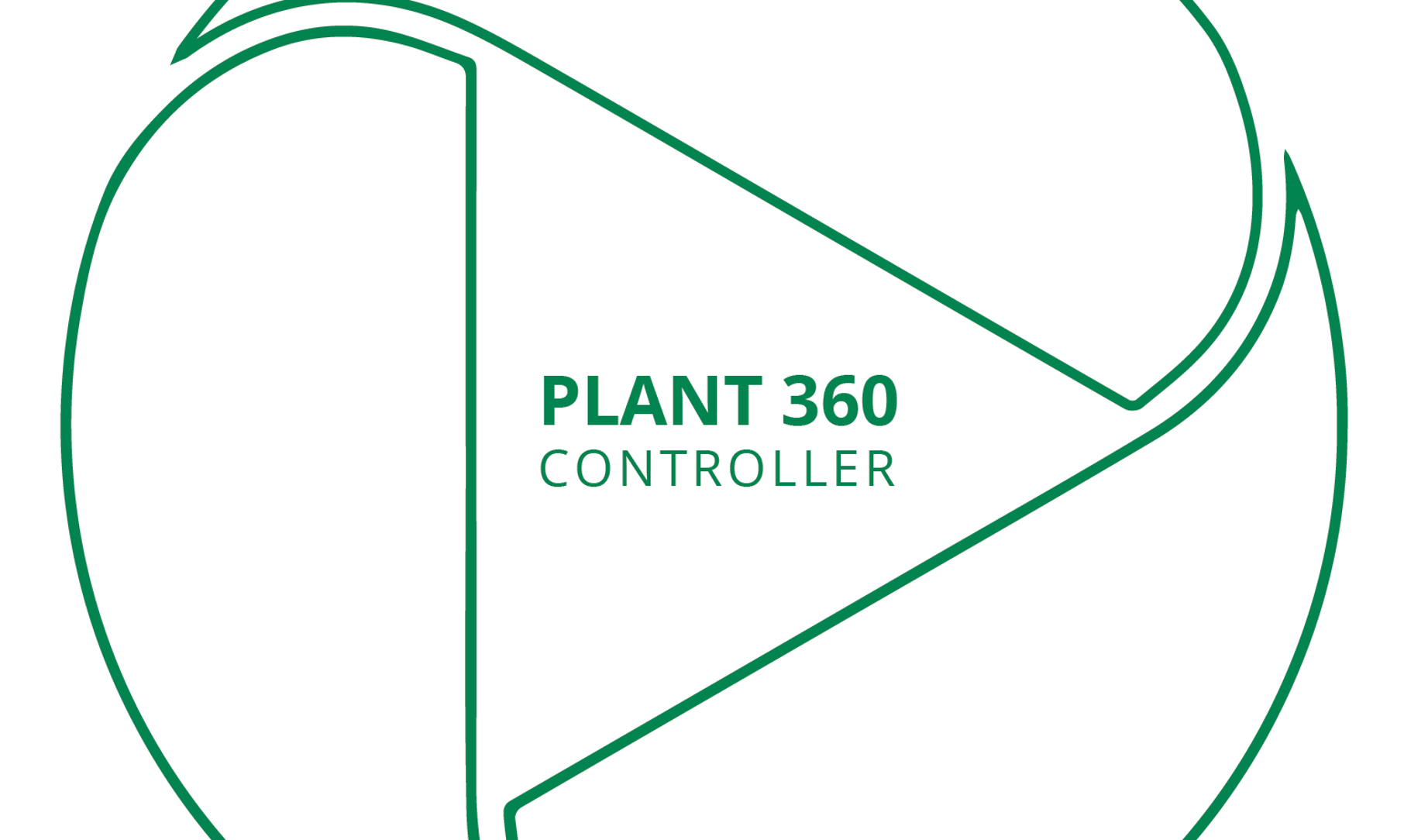
Smart water use
Within manufacturing, water serves a host of purposes: from cleaning and transportation of materials, to sanitation and housekeeping – like supplying drinking water to staff. As such, industries not only consume a lot of water – accounting for approximately 22% of total global use – but also misuse a sizeable amount, with 80% of wastewater released back into the environment without being adequately treated.
Small but effective changes could simply involve teaching employees to be more aware of how to save water and even identify problems, or by installing water meters on the factory floor. Another recommendation would be to install wastewater management systems or filling machines which are continually pushing the boundaries when it comes to water efficiency. Like our third-generation filling machines, which can now be fitted with water reduction conversion kits designed to cut overall consumption by up to 50%.
Letting go of waste
A great way to reduce waste output is to use more sustainable packaging: at SIG, we make all our aseptic carton packaging using minimal materials that are recyclable. In addition, every single carton pack is produced entirely using renewable energy, an industry first. By ensuring our products are sustainable, we make it easier for our customers to control the carbon footprint of every source they use.
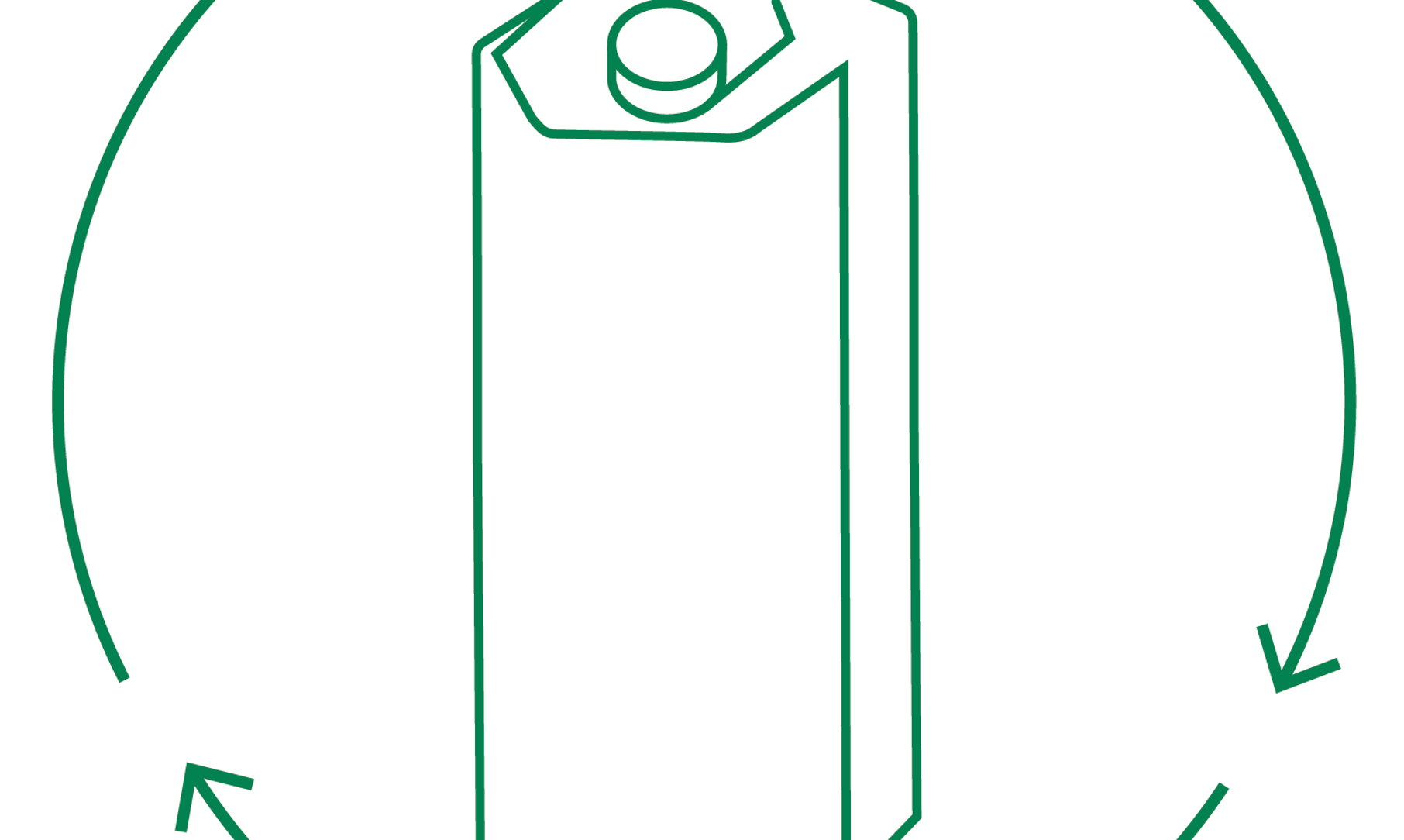
Another big factor in tackling waste is prevention, i.e., carrying out regular checks on machinery in order to reduce downtime, as well as finding innovative ways to reuse as many by-products as possible. This could include repurposing by-products, sending excess materials back to suppliers, or, on a basic level, introducing a waste management system that ensures all waste is separated correctly before being disposed of. At SIG we are at the forefront of waste-reduction technology, with our filling machines offering clients a waste rate that comes in at just under 0.5% – the lowest in the industry.
Overall, by focusing on these four areas, manufacturers can work towards more long-term, sustainable practises.
In part five we’ll tackle carbon emissions and look at what various industries are doing to reduce their carbon output as much as possible. What role do sustainable factories play in this ambitious goal, and what long-term benefits could this lead to?
Want more stories in the series sent straight to your inbox? Subscribe to the SIGnals Update, our exclusive bi-weekly newsletter.
- tháng 4 26, 2021