What’s new with the smart factories of today?
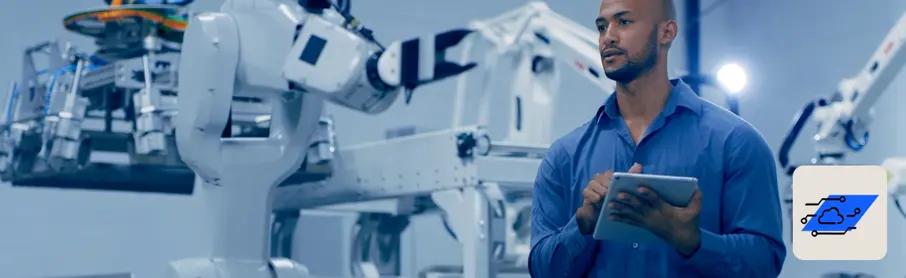
Smart factories: a status update
Automation, predictive maintenance, data collection, and real-time tracking and traceability. These are just a handful of the doors digitalization has opened for the food and beverage industry. But what do those changes mean on the ground, and how much further can we go?
The information game
One of the more notable effects of digitalization has been an improvement in data collection in terms of speed, accuracy, and amount. For manufacturers, this has led to a range of benefits: from being able to monitor the temperature of perishable goods across every step of the supply chain – thus, reducing food waste and health risks for consumers – to, quite simply, being able to harvest all the data at their disposal in the first place.
The proof is in the pudding
At Bells of Lazonby, a large-scale manufacturer of breads and baked goods, employees are being joined by ultrasonic cutting robots capable of slicing cake into a limitless number of shapes and sizes. As well as saving operators from having to manually change cut patterns – allowing them to spend their time on other tasks – the robots have helped reduce food waste while improving production time.
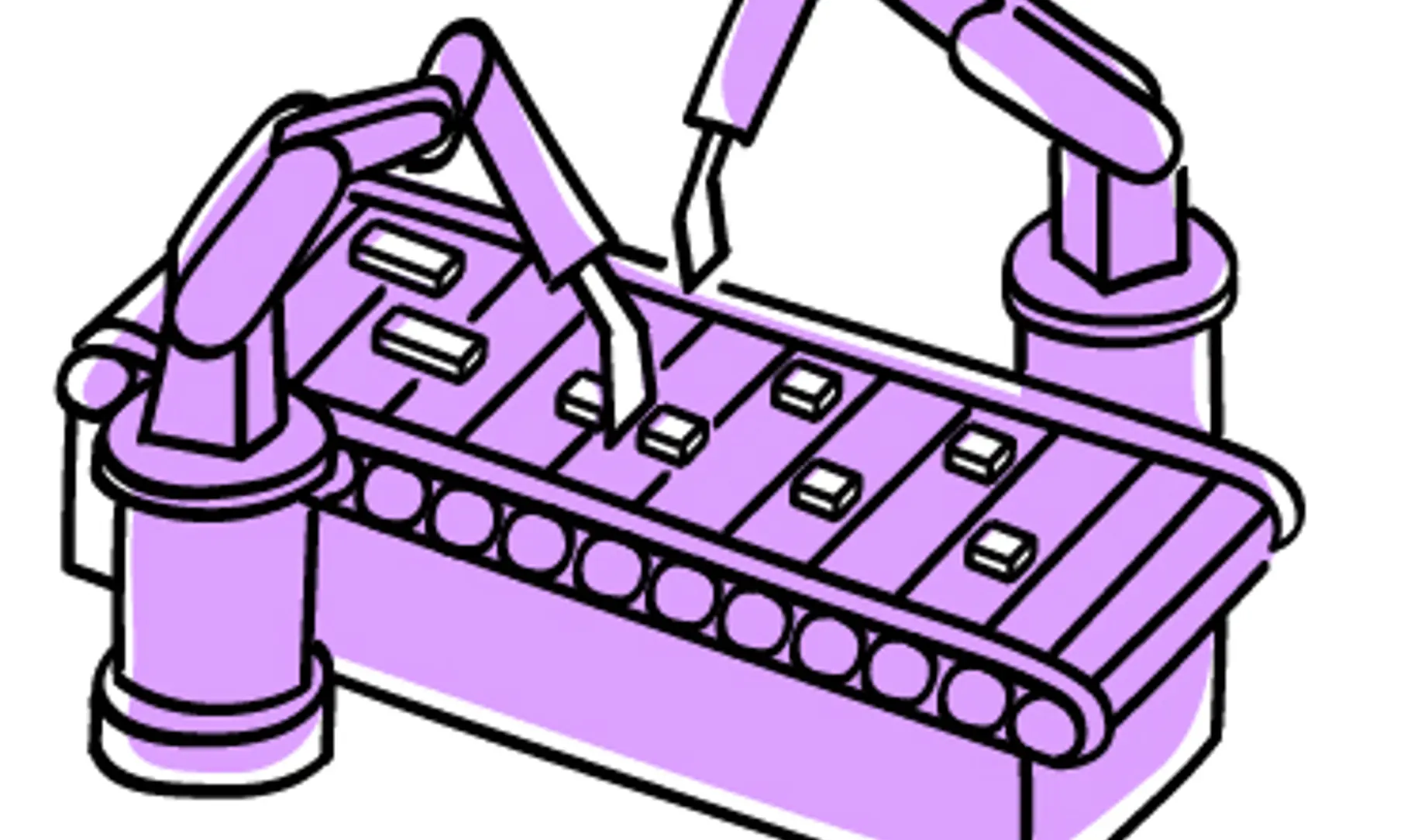
Using digitalization to drive sustainability
Via the possibilities offered by the Internet of Things, it is now easier for manufacturers to switch to a more service-based approach when it comes to production, meaning less waste. What’s more, other digital offerings such as advanced analytics, 3D printing and machine learning are also helping the food and beverage industry – and other industries – promote the idea of a circular economy.
Clearing the way to better standards
By way of example, if we look at blockchain, this can help food and beverage manufacturers track where materials come from so they can make more informed decisions about their suppliers. And with condition-based monitoring becoming more and more efficient, this can help further improve machine uptime and even health and safety on the factory floor.
What comes next?
We’ve already seen how much of an impact digitalization has had on today’s smart factories. So, what comes next – and how much more can we do? With various studies showing how much smart manufacturing could boost the world economy, this is a trend that will not slow down any time soon.
The same goes for the solutions being developed to make smart factories even smarter. Whether it’s our range of flexible filling equipment solutions or our digital solutions that include SIG Asset Health Monitoring, SIG ECS and SIG Line Monitoring – all of which are designed to work in tandem to both help manufacturers collect data 24/7 and easily understand and utilize it.
In part four of the digital drive, we focus on how digitalization has transformed the last link in the food and beverage supply chain – the retail industry. How are supermarkets and other establishments selling food and beverage products using technology to change the way consumers shop? Follow this story and more by subscribing to SIG Newsletter.
- 12月 21, 2023
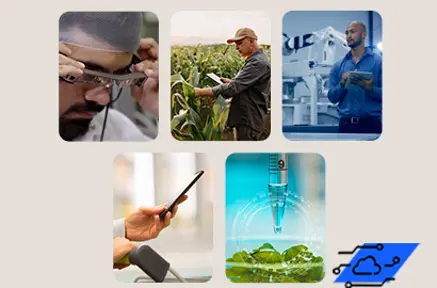
A look back at the forces driving digitalization
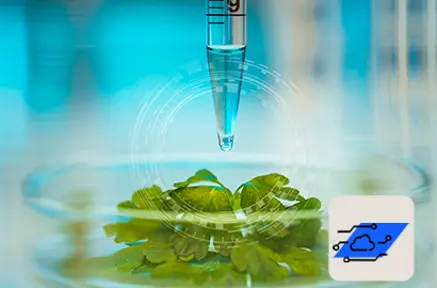
How digital technology is shaping what we eat
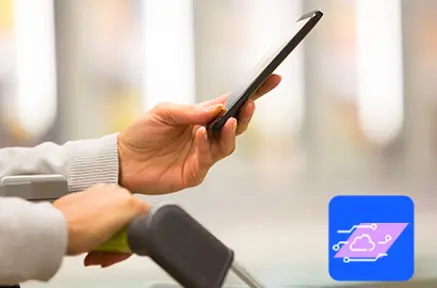