The aluminum account
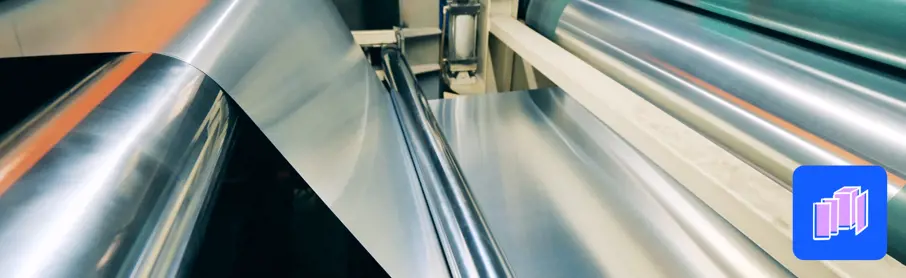
An integral part of our daily lives today, aluminum is present in everything – be it our appliances, electric fittings, cars, takeaway containers, or that roll of foil hiding in the kitchen drawer. This omnipresent silver metal is however among the newer natural discoveries and dates back less than 200 years.



The history
The discovery of aluminum is anything but straightforward. As the metal is not found in nature in its pure form, it needs to be separated through a chemical process. And many scientists played pivotal roles in the journey to finding the ideal process. From 1825 when the metal was first isolated in a lab through electrolysis to 1885 when the first industrial aluminum was produced and then to 1886 when a cost-efficient production method was discovered in different parts of the world at the same time. Three years later, an Austrian chemist invented a method for extracting aluminum oxide from bauxite.
Together, the Hall-Héroult process and Bayer process transformed how aluminum was perceived and led to the widespread adoption of the material. Till date, both the processes are integral to aluminum production.
The process
Aluminum production involves three key stages. The first stage is mining of bauxite, the most common ore of aluminum. In the second stage, the bauxite is refined into alumina or aluminum oxide using the Bayer process and finally, pure aluminum is extracted from it via the Hall-Héroult process using electricity. The final stage is also called smelting. At the end, 1 ton of aluminum can be extracted from 4-5 tons of bauxite.
The prevalence
Transport, construction, electricity, consumer goods – there is virtually no industry where aluminum is not used in some form. Its widespread adoption is owing to its properties of low density, electrical conductivity, strength-to-weight ratio, malleability, and recyclability, among others. The prevalence of aluminum in food and beverage packaging is also because of its exceptional barrier properties that blocks out light, oxygen, and moisture.
The challenges
It is a fact that aluminum makes up more than 8% of the earth’s crust but the complicated procedure of extracting the metal does not come without environmental challenges. From the toxic byproduct, red mud, to extensive energy use – the environmental impact of aluminum production can be substantial. The carbon footprint of aluminum production amounts to about 3% of the global industrial emissions, with smelting being responsible for the highest share in the supply chain.
The Aluminium Stewardship Initiative (ASI) is working actively towards reducing the emission significantly by requiring smelters to cut emissions to below 8 tons of CO2 per ton of aluminum produced by 2030. Therefore, it is important to use only ASI-certified aluminum like we, at SIG, have been doing for years now for all our packaging that have a thin aluminum layer.
The road to recycling
Recycling of aluminum requires only 5% of the energy needed for raw aluminum extraction without the massive impact of toxic byproducts. And with aluminum being infinitely recyclable, it is crucial that the material doesn’t end up in landfills. But that is easier said than done, especially for single-use aluminum food and beverage packaging like takeaway containers and aluminum foil. And although almost 70% of aluminum cans used globally are reportedly recycled, the environmental impact of the remaining 30% cannot be discounted – making it imperative for organizations across the world to step up recycling initiatives.
The alternative
Today, reducing one’s carbon footprint is top of the mind for both consumers and businesses. No wonder they are looking for alternatives to aluminum too, be it in an everyday material they can use for baking and cooking or food and beverage packaging. Even aseptic cartons till recently had a thin layer of aluminum and was considered essential for food safety. But we, at SIG, pioneered the world’s first aseptic carton with no aluminum layer. This industry-first solution has a carbon footprint up to 27% lower than standard SIG packaging material and offers full barrier properties of standard aseptic cartons with shelf stability for even oxygen-sensitive products.
Throughout the series, we have delved into different packaging materials. If you missed any of it, watch out for our next post where we are going to revisit all the materials or subscribe to our exclusive bi-weekly newsletter to get the summary in your inbox.
- 9月 20, 2023