Service that delivers
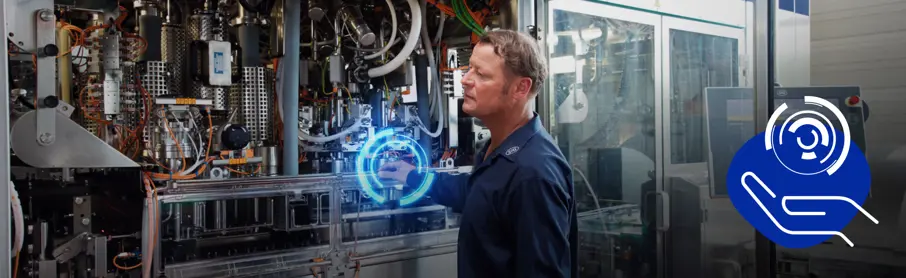
Effective and timely service plays a vital role in manufacturing. In the first part of At Your Service, we explore how this can help optimise plant production.
Machinery without service support is a risk no manufacturer should willingly take. When it comes to an entire production plant, the stakes become even higher. This is especially true for food and beverage production where even minor breakdowns can result in plenty of food waste, not to mention time-consuming interruptions within the supply chain.
Therefore, when it comes to service solutions and choosing a packaging partner, both quality and speed of response are highly important. Here, the packaging partner needs to be a hands-on stakeholder and not just a supplier: from suggesting the right solutions for a manufacturer’s specific needs all the way to installation, training, and beyond.
The science of good service
At SIG, we believe in great service solutions and in supporting manufacturers before, during and long after they choose to work with us. From offering basics such as maintenance and technical support, to our value-added service solutions designed to improve machine availability, optimise performance and help manufacturers embrace digitalisation. In summation, our portfolio of comprehensive services covers every aspect of food and beverage production.
Smooth sailing
With all the above under our belt, it stands to reason part of our service to clients means being there for them when the unexpected happens. Thus, with the onset of the COVID-19 pandemic in 2020, we were more than prepared to help our clients overcome a host of challenges en route to the next normal.
Ready, set – accelerate
Another part of our service involves showing our faith in client’s ideas from the very beginning. Take Accelerator, a modular marketing services solution aimed at helping food and beverage manufacturers launch innovative products quicker and with better results – all while keeping costs low. Similar programs include SIGCUBATOR, which aims to help small companies, start-ups and entrepreneurs with everything from testing prototypes to market launch.
Your end-to-end partner
We can deliver high-quality original spare parts quickly and easily so your SIG filling machines, applicators and selected downstream equipment can work better for longer. We also offer training programs that cover everything from boosting your employees’ knowledge levels to equipping them with the skills to optimise production. In addition, our most recent tech centre opened in China in 2019 and is designed to help clients speed up development and implementation of new product concepts.
Going digital
Last but not least, at SIG we’re big on going digital – for good reason. With Plant 360 Asset Management, optimise filling line availability and reliability from anywhere, at any time – without breaking your budget.
In the second part of At Your Service we will look further into Plant 360 and other solutions that utilise digitalisation to help improve efficiency and productivity. Both of which are especially important when it comes to supporting clients from a distance, and both of which lead us to the core of our upcoming piece: with the pandemic forcing many people to work remotely, how did SIG help? Don’t miss our take – subscribe to our exclusive bi-weekly newsletter the SIGnals Update for this series and many more.
- 9月 24, 2021