Putting the green in production
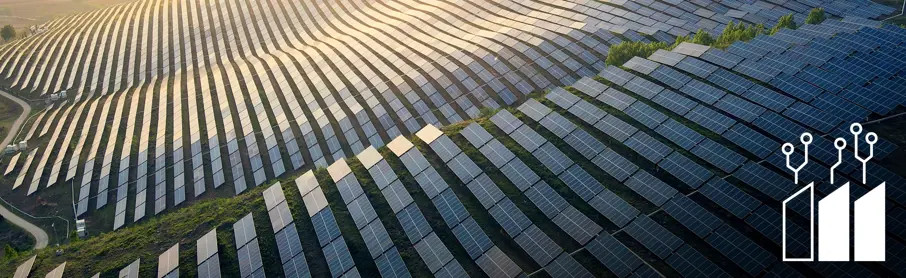
In part five of Ultimate Factories, we examine how manufacturers are prioritising sustainability on the factory floors in more ways than one.
In the recent years, the environmental effects from the industries have become a major concern. And in a bid to make manufacturing more sustainable, multiple regulations and recommendations have emerged. In response, industries are making a headway, and even leading the transition as they work towards carbon neutrality in their production facilities.
In our earlier Sustainable Factories series, we examined the steps manufacturers can take to build and run factories with minimal environmental impact – from smart water use and waste management to renewable energy and optimisation of resources. However, how are these steps being implemented in the factories, including our own?
A journey to green manufacturing
Green production is not a short-term goal. It is a journey that often consists of small steps a manufacturer takes to make their production process more sustainable. And every bit matters. Ideally, a sustainable factory would have optimised processes that minimise negative environmental impacts, conserve energy and natural resources while ensuring the safety of employees, communities and consumers.
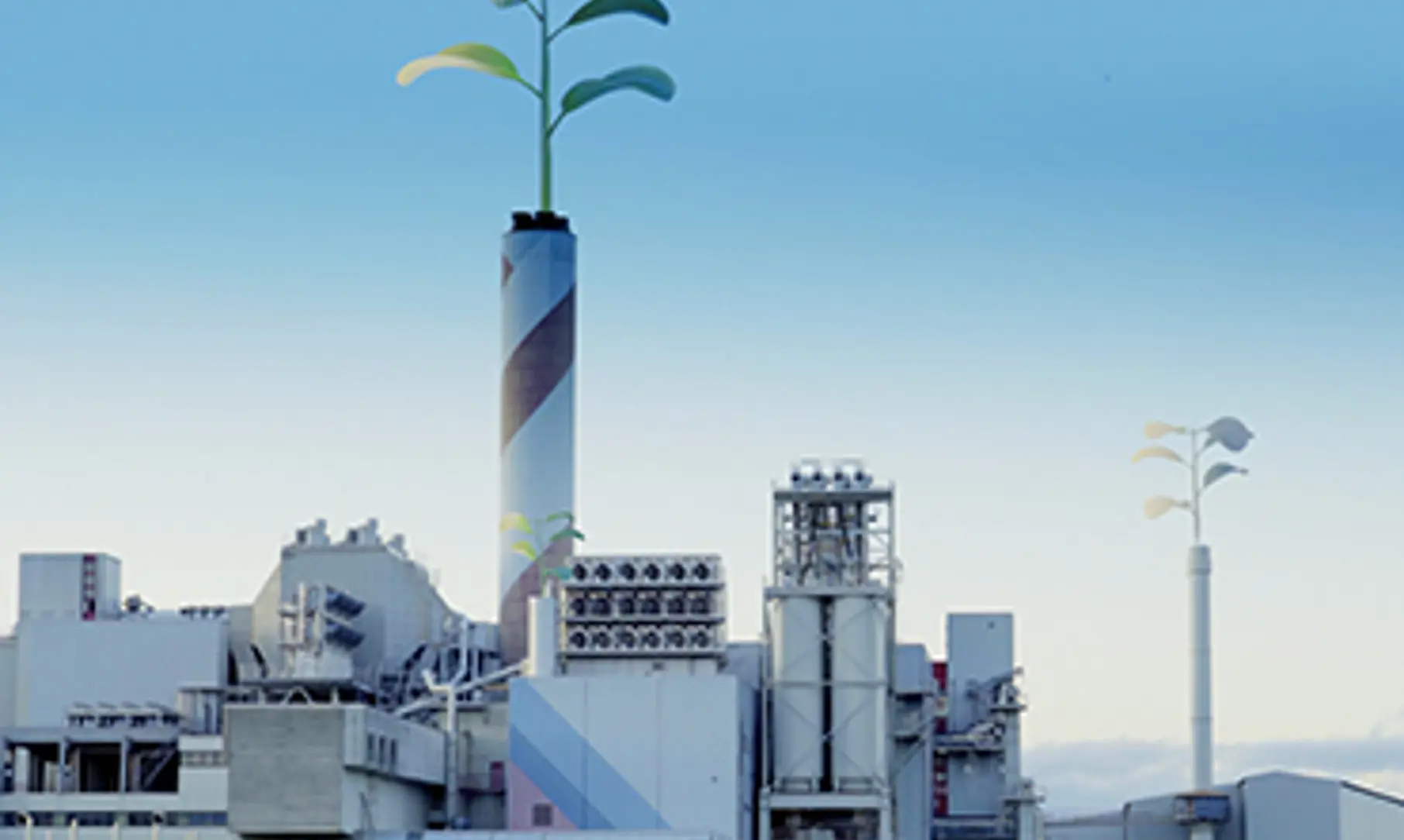
A sustainability-first plan
Inaugurated in 2020, SIG’s new factory in Suzhou, China is designed to have lowest possible carbon emissions by prioritising a sustainable approach at the planning stage. Features like photovoltaic panels on the roofs generate 1.5 million kWh solar energy while custom lighting systems reduce electricity consumption. Furthermore, rainwater harvesting, and reuse help save 28 million litres of water every year.
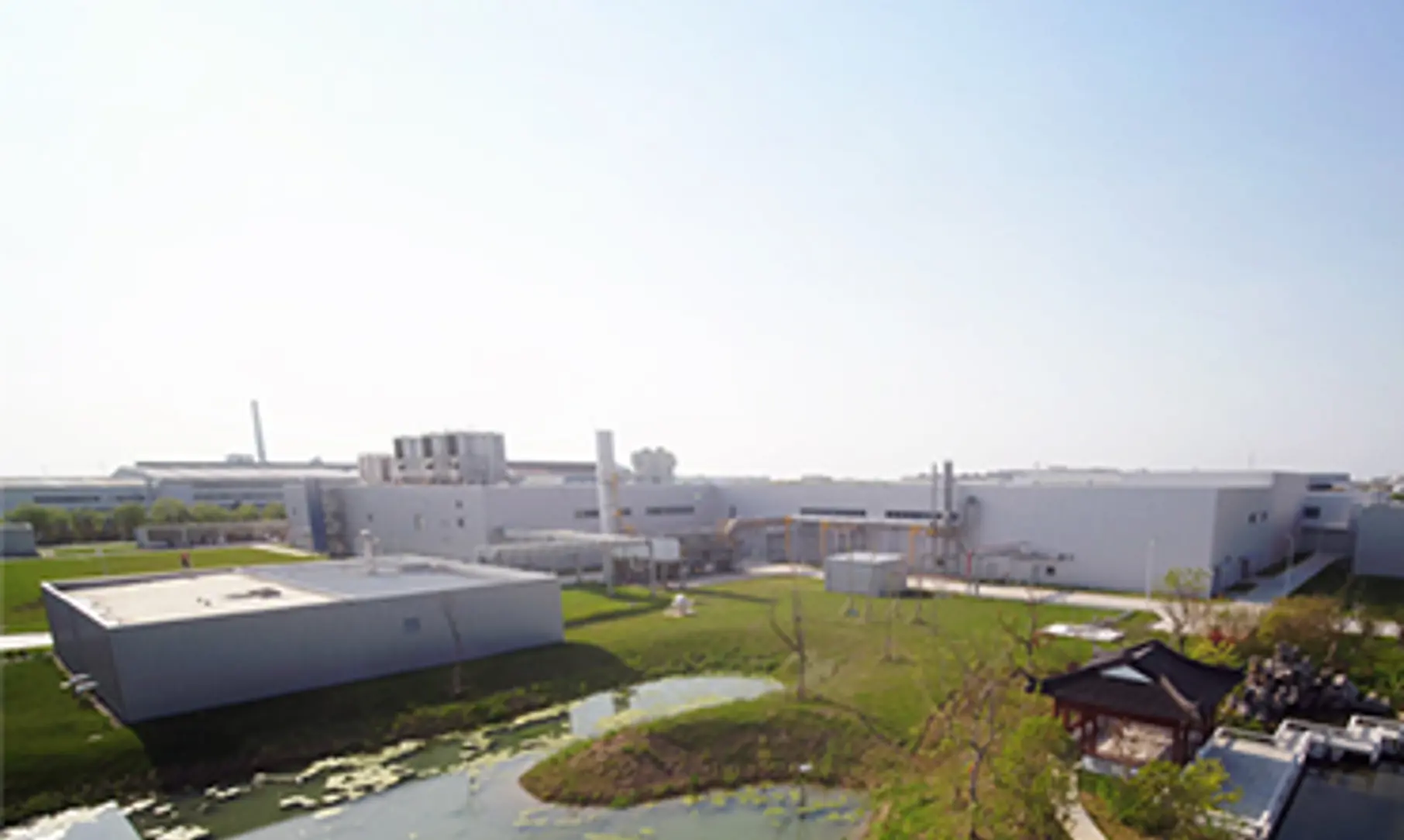
Awarded LEED Gold certification – a high level of recognition for green buildings, this SIG factory shows how environmental, safety and operational performance can be achieved right from the start.
Sustainable at source
Fair Cape Dairies in Cape Town, South Africa believes in doing the right thing every step of the value chain. Since 2018, the dairy farm has been working off grid for its milking operations during the daylight hours. The water used in the milking parlour is also recycled for irrigation at the farm to save nine million litres of water a month. They target to take these green practices to their production facilities next.
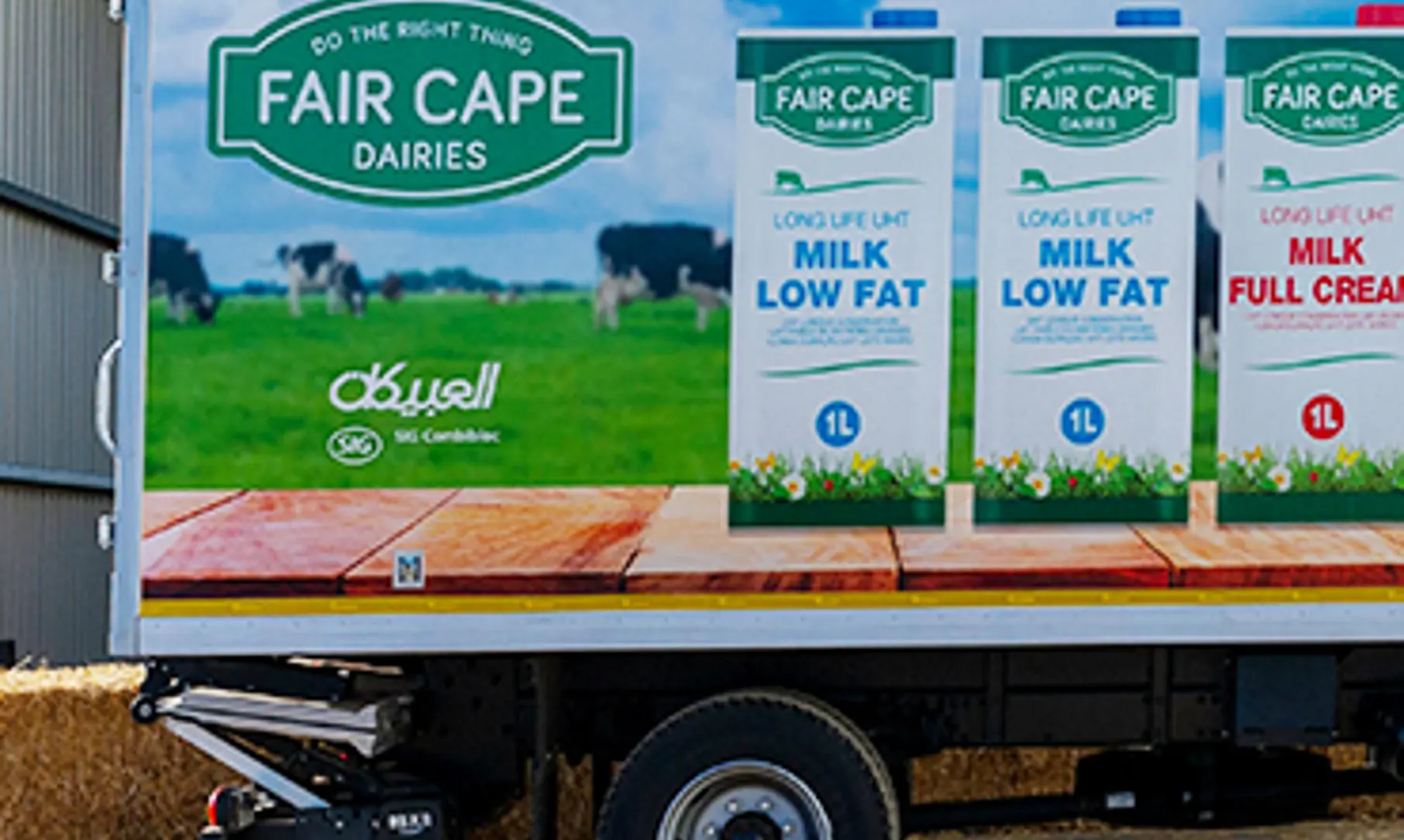
Leading the transition
As regulatory bodies and businesses around the world are taking steps to transform operations, SIG has already achieved carbon neutral production by transitioning to 100% renewable energy at our production plants. We have also surpassed our target to halve operational emissions by 2025 and accelerated our timeline for climate action with greenhouse gas reduction targets approved by the Science-Based Targets Initiative.
A move towards green manufacturing involves the entire production process in the plant and choosing right partners across the supply chain. Reach out to explore how we can support you in your transition to green manufacturing.
In the next and final part of this series, we will look back at the different factors that make a factory stand out, helping manufacturers achieve more and see what lies ahead in the world of smart manufacturing. To get this story and other interesting insights relating to the food and beverage industry across the world, subscribe to our exclusive bi-weekly newsletter, SIGnals Update.
- 11月 24, 2022