The paperboard plot
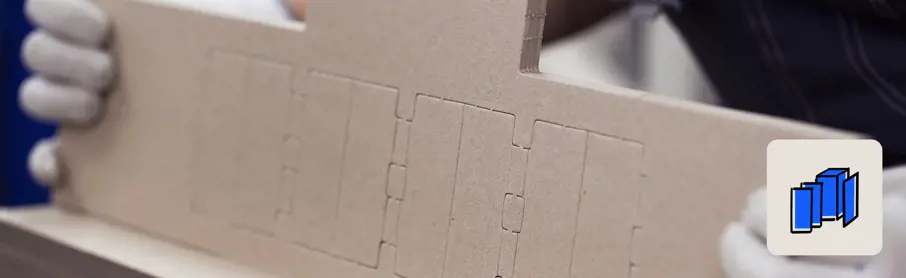
Paper-based packaging has a rich history, spanning centuries. Paperboard itself can be traced back to the early 1800s. A 100 years later, John Van Wormer created the first milk carton as a paper bottle. Perga cartons developed by Jagenberg Werke, the origin of today’s SIG carton business, were the next in line. Both these cartons were made of paraffin coated paperboard to prevent leaks.
Since then, beverage cartons have come a long way to offer the high level of food safety and shelf stability that we take for granted today. Protective layers of different materials, including paperboard, make it all possible. Liquid Paperboard (LPB), accounts for 70-80% of the total weight of a beverage carton and is crucial for its rigidity.



The material
Paperboard, simply put, is thick paper with grammage over 150 g/m2. Made as both single-ply and multi-ply, paperboard is light, rigid, and easy to fold, making it a widely popular packaging material. Modern LPB is a multi-ply paperboard made from virgin fibres and often coated for good printable surfaces.
The process
The science of papermaking can be traced back to Han dynasty in ancient China where the first sheet of paper was sieving, pressing, and drying a mixture of mulberry tree fibres and water. Interestingly, the basic process is still somewhat similar after centuries. Today, the papermaking process begins with short logs, wood chips or even recycled paper.
For LPB, only virgin wood chips are used. In the pulp plant, wood chips are pulped through a chemical cooking process or through a thermo-mechanical refining process before being optionally bleached. The fibres are then washed and refined before being fed into the board machine
In the next stage, on the board machine, a mixture of water and pulp is poured onto a moving screen. The water drains through the screen, leaving behind a wet layer of wood fibre which forms the sheet. Modern machines combine several sheets to form a multi-ply paperweb, which then goes through sections where water is removed by pressing and drying. Next, the surface of this paperweb is typically coated with a layer of clay. In the subsequent reeling and winding process, the big paper machine reels are cut into smaller sized LPB rolls.
These LPB rolls are then further processed to create beverage cartons. At SIG, we add in additional sealing and barrier layers using an extrusion line before printing and forming carton sleeves.
The types
Paperboard is a highly versatile material used in packaging a variety of products and comes in different grades, each with unique properties. Solid bleached sulphate (SBS) has a clay-coated surface and is the preferred choice for food and beverage packaging, coated unbleached kraft (CUK) is the norm in heavy-duty packaging and coated recycled paperboard is mostly used for packing non-food and dry foods, such as pasta and cake mixes.
Beginning to end
Wood chips, the primary raw material used in making paperboard for LPB, are a renewable resource, especially with sustainable forestry ensured by organisations like Forest Stewardship Council™ (FSC™). Containing a great proportion of long cellulose fibres, paperboard is considered high value in the recycling stream. Being lightweight, it also helps lower the footprint of transportation and storage when used in packaging. At SIG, we not only use FSC™-certified paperboard (FSC-C020428) for our LPB but are also working actively to increase recycling rates through different initiatives .
Innovation taking it further
Paperboard suppliers are driving innovation further by optimising LPB for stiffness utilising advanced technologies such as multi-layer construction, different types of fibres, and the use of Microfibrillated cellulose (MFC). This optimisation allows for the use of less raw material without compromising the technical properties of the LPB.
In the next part of our series, we will turn our focus on one of the most-discussed packaging materials in history – plastic. Keep a lookout for the next edition of Material Matters or subscribe to our exclusive bi-weekly newsletter to get the story in your inbox.
- Juni 08, 2023