Service from afar
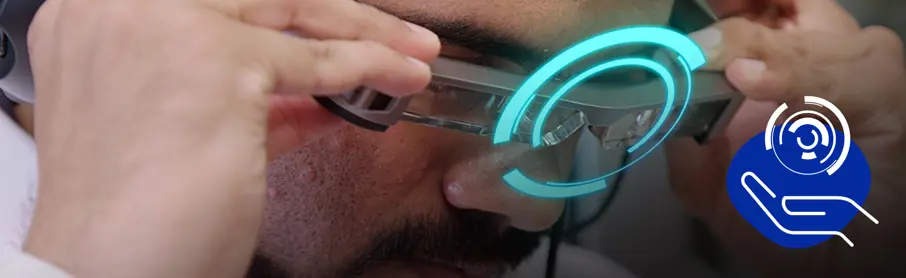
Great support is one thing. Great support that can be delivered remotely … is another. In part two of At Your Service, we discuss the relevance of remote service solutions in a post-COVID world.
Being on the ground in your factory is a great way of understanding how things are going. But there are some things only remote solutions can help with, such as the convenience of tracking every machine at the touch of a button from wherever you are in the world – and at any time.
You don’t have to dig much deeper to uncover the other benefits that come with remote service solutions: from the ability to carry out condition-based monitoring, all the way to lower cost of ownership – and a whole lot more in-between.
The COVID challenge
As touched upon in our introductory piece, the pandemic forced a lot of the world’s workforce to stay at home – highlighting the importance of remote support. In April 2021, more than 60% of the US workforce worked remotely. Today that number has dropped a little but still remains considerably high, indicating a need for manufacturers to follow suit and embrace remote services.
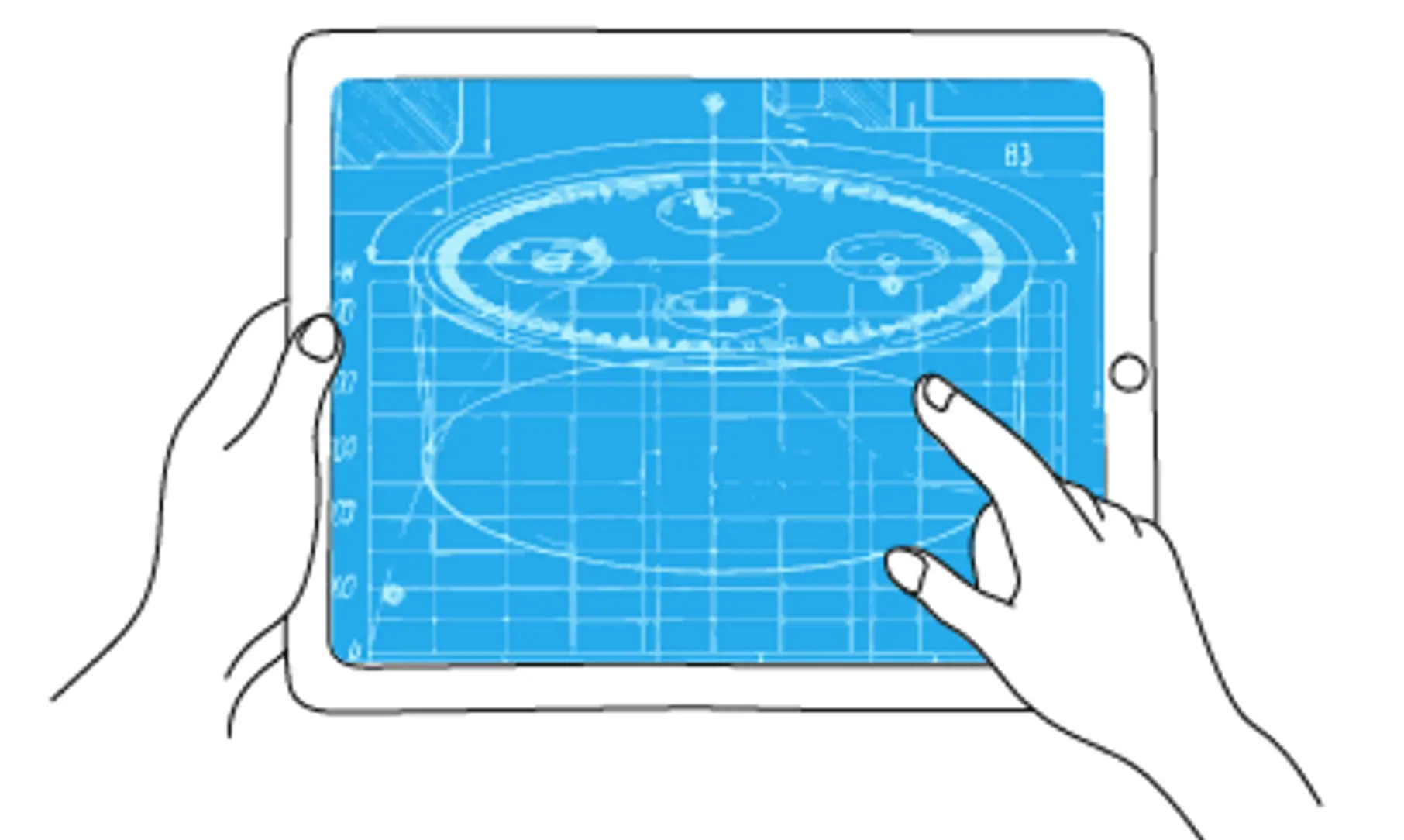
However, large-scale adoption of remote services does face some barriers, with manufacturers worried about integration costs and cybersecurity risks, among other concerns. And so, to help clients embrace a more digital world takes a partner who can give them the confidence to move forward. At SIG, we’ve been working around the clock to keep our clients operating as close to normal during the last year and a half.
Through the (remote) looking glass
In 2018 we launched Remote Services to help food and beverage manufacturers service their filling machines more efficiently and improve uptime. With Remote Services, our clients can connect with an SIG expert from anywhere in the world, whenever they need to – using the video-enabled smart glasses that come as part of the package.
Not only does this result in issues being solved faster, it helps manufacturers adopt more sustainable practices: according to SIG MEA, between the second quarter of 2020 and second quarter of 2021, clients who used our Remote Service solution saved a total of 15 tons in CO₂ emissions by dealing with problems over video chat – instead of bringing an expert in.
See our Remote Service solution in action
Milking every opportunity
As another example we’ll refer to LACBOM, a Brazilian dairy company and SIG client. One year into the pandemic LACBOM acquired our Remote Services solution to improve filling machine uptime and reduce overheads, thereby absolving themselves of the need to pass increasing costs onto clients. To find out more about how we helped LACBOM, download the case study here.
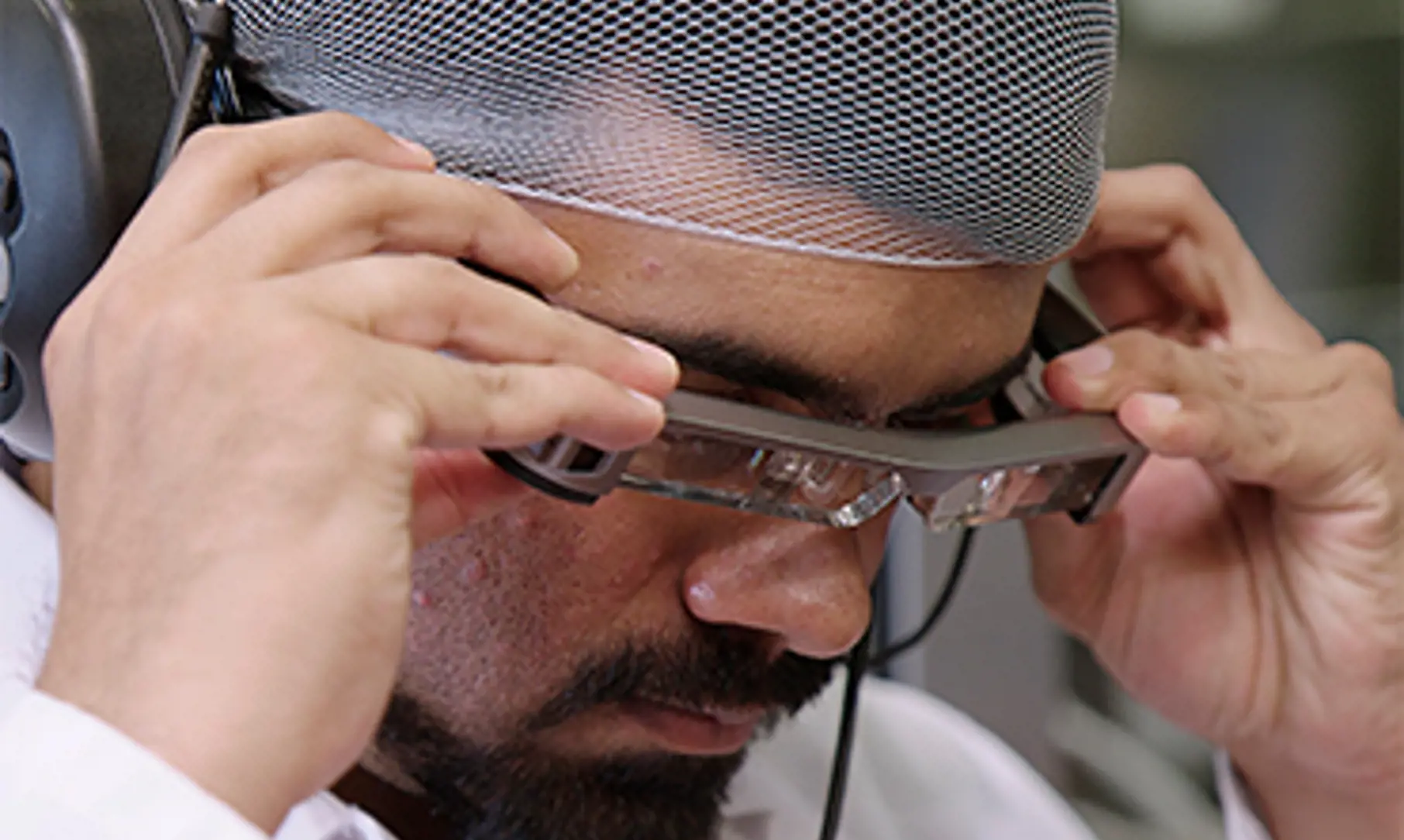
In the third part of our series we’ll cover monitoring. Specifically, how optimal monitoring can support sustainable factory models – and which of our support solutions can help manufacturers get the job done.
To follow this series and more, don’t forget to subscribe to our exclusive bi-weekly newsletter the SIGnals Update.
- Oktober 27, 2021