Focusing on flexibility
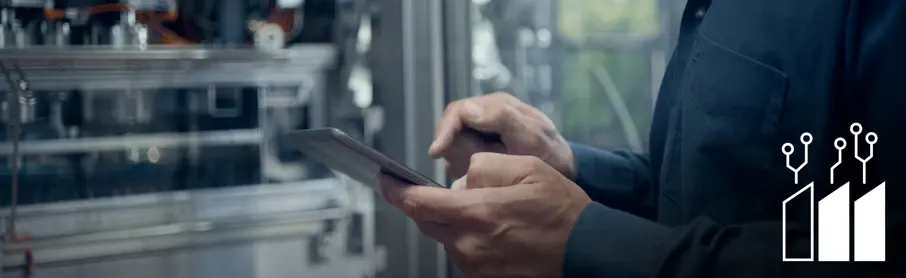
In part four of Ultimate Factories, we discuss the importance of flexibility in production, and how it is emerging as a key factor in meeting market demands.
Manufacturing has come a long way since the time when Henry Ford said, “A customer
can have a car painted any colour that he wants, so long as it is black." Interestingly, even though the company stuck to this policy for over 10 years, Ford still accounted for more than half of the world’s registered cars in early 1920s.
The consumers of the 21st century, however, expect products to match their requirements in all industries, from automobile to food and beverages. And this makes flexibility a top priority for manufacturing leaders. But what does flexibility translate to on the factory floor and how is it transforming businesses, especially in food and beverages?
A key factor
Simply put, flexibility in manufacturing is the ability to change aspects of a production line based on the need of the hour, be it market demand, changes in supply chain, or unprecedented challenges. Manufacturers adjust their production to factor in changes within varied aspects such as flavours, nutrients, allergens, sizes, or formats. And the flexibility to make these adjustments also helps them to differentiate their offerings by meeting shifting market demands.
A case of market-centric production
Beyti, one of the largest producers of milk, juice, yoghurt, and creams in Egypt, is catering to a market of 86 million consumers. Meeting the requirements of such a large and varied consumer base comes with its challenges. And therefore, this joint venture between Almarai and PepsiCo works with SIG in their award-winning factory, leveraging the full benefits of flexibility in production and packaging.
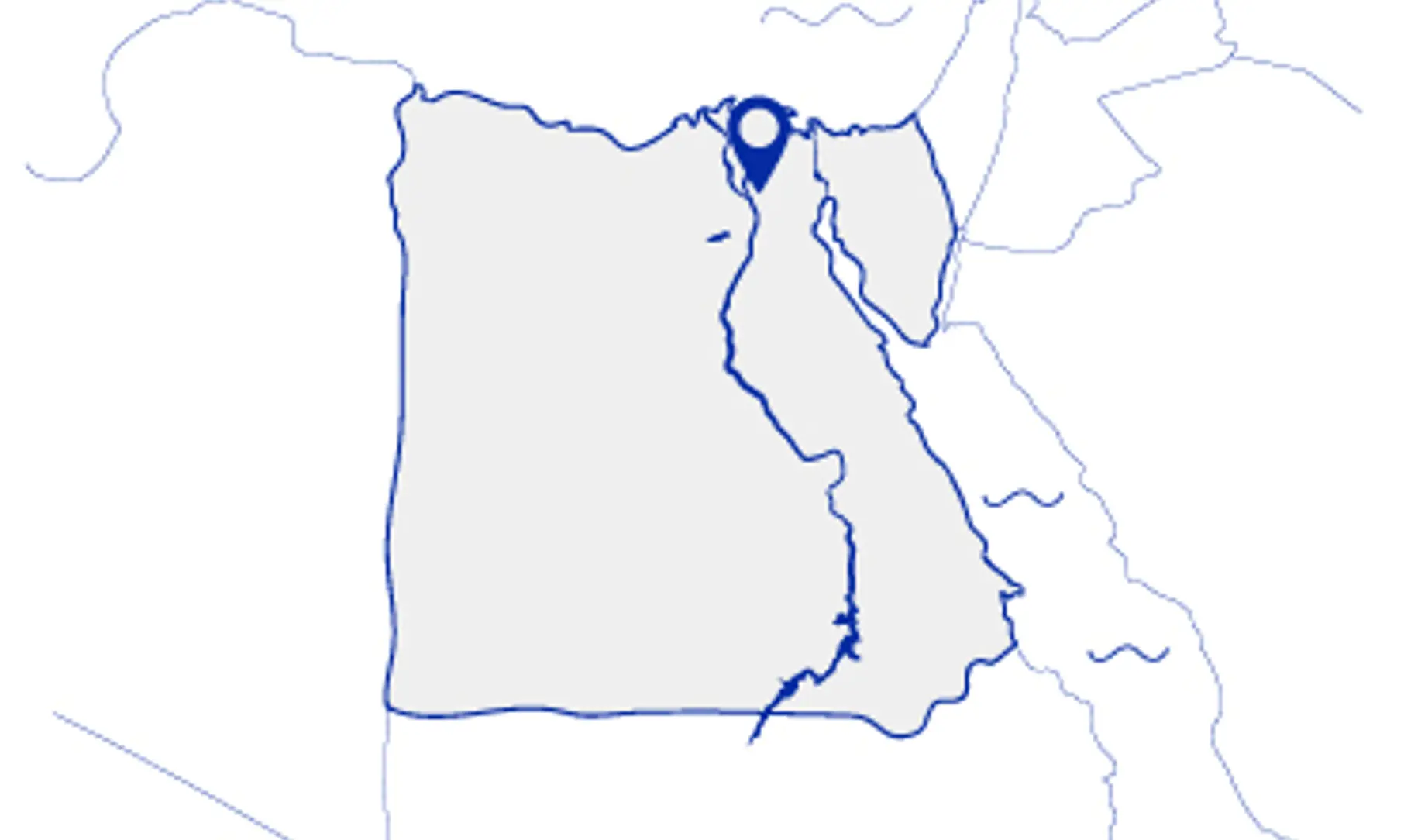
With size, product, and format flexibility of SIG filling lines, Beyti produces six brands in four segments in varied sizes. And by the end of 2022, they are adding more SIG filling lines to meet increasing market demands flexibly in more categories and segments.
A new stride in state-of-the art digitalisation
Hochwald, one of the leading German dairy cooperatives recently opened the door to its new Mechernich plant, the largest European greenfield project in UHT milk. The mega plant is operating with 15 SIG filling machines enabling Hochwald to offer a varied selection of aseptic packs in five different formats, with a range of volumes, closures and paper straws.

“SIG has helped us make unique end to end digital solutions a reality at our new mega plant, taking our full plant automation to the next level and its fast and flexible filling technology will ensure we fulfil our consumers’ desire for more differentiation, as well as meet the changing demands of retail.”
Thorsten Oberschmidt
COO, Hochwald
End-to-end digital solutions for connectivity and monitoring in this new smart factory is geared towards ensuring operational efficiency and quality control while maintaining agility in formats, volumes, and sizes.
What’s more?
Digitalisation and flexibility go hand in hand. At SIG, therefore, our portfolio of digital solutions take into account every facet of manufacturing while our flexible filling technology ensures that manufacturers can meet market demands without compromising on speed, efficiency or quality.
It goes without saying that sustainable packaging is among the top asks today. And with SIG you can extend flexible production to even the choice of packaging materials, choosing from our wide range of sustainable packaging solutions to meet the varied sustainability demands across the globe. In the next part of the series, we will delve into how sustainability is a driving force on factory floors too. Don’t miss the next post and other insights – subscribe to our exclusive bi-weekly newsletter, SIGnals Update.
- Oktober 27, 2022